Alles, was Sie über zerkleinerten Granit wissen müssen
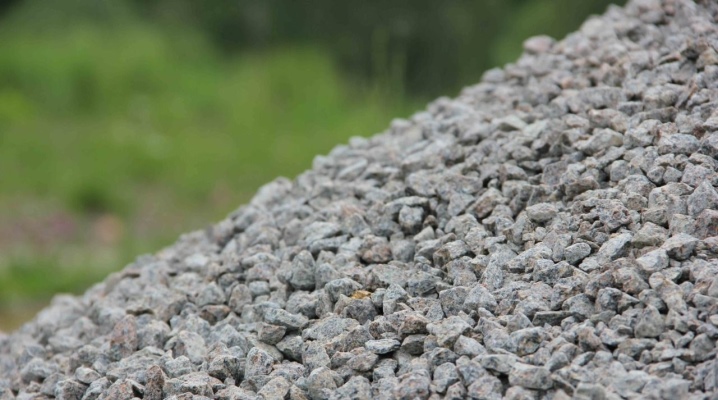
Granitschotter ist die gebräuchlichste Art von Baumaterial, er wird aus Vulkangestein gewonnen, das eine erhöhte Festigkeit und eine körnige Struktur aufweist. Der Farbton kann fast beliebig sein, alles hängt von der Zusammensetzung ab. Naturgranit ist ein besonders langlebiger und harter Stein.
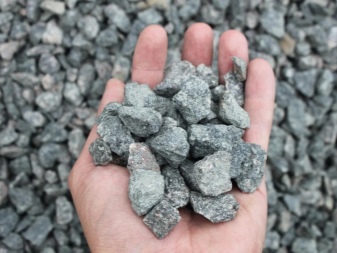
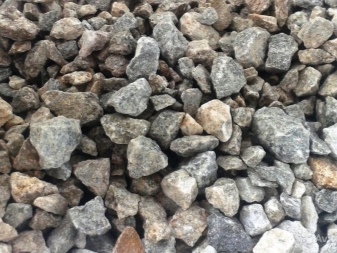
Vorteile und Nachteile
Vorteile von Granit.
- Erhöhte Festigkeit und Härte - dieser Naturstein hat den höchsten Koeffizienten.
- Einfache Verarbeitung, da es gut mit verschiedenen Haftkomponenten interagiert.
- Praktisch - geeignet für den Einsatz in verschiedenen Bereichen und Branchen.
- Aussehen - Granitschotter sieht aus wie ein Stein mit vielen Einschlüssen von schwarzen, grauen und weißen Farben, eine solche spezifische Farbe wird oft für dekorative Arbeiten verwendet.
- Geringe Wasseraufnahme - diese Eigenschaft spielt beim Bauen eine wichtige Rolle, da sich Granit durch Feuchtigkeit nicht verformt.
- Frostbeständigkeit.
- Haltbarkeit.
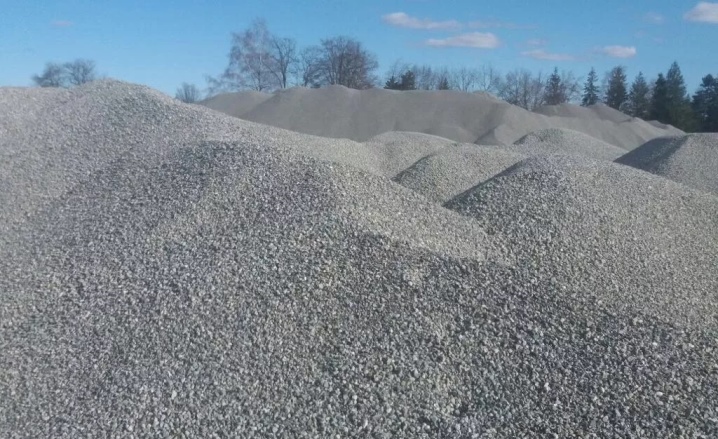
Nachteile von Granit.
- Im Gegensatz zu Dolomitschotter, dessen Härte- und Festigkeitskoeffizient mit Granit identisch ist, hat der zweite einen höheren Preis. Dies ist der Hauptnachteil des Materials.
- Ein mühsamer Herstellungsprozess, nach der Gewinnung aus einem Steinbruch sind zusätzliche Schritte erforderlich.
- Umweltfreundlichkeit - Granitschotter kann schädliche Bestandteile enthalten, im Gegensatz zu Kalkstein, der eine geringere Radioaktivität aufweist, obwohl beide Gesteine natürlichen Ursprungs sind. Wenn Sie einen bestimmten Schutt auswählen, müssen Sie die Zertifikate durchsehen und eine Radioaktivitätsklasse auswählen. Es ist besser, die Granitsorte beim Bau von Wohngebäuden nicht zu verwenden.
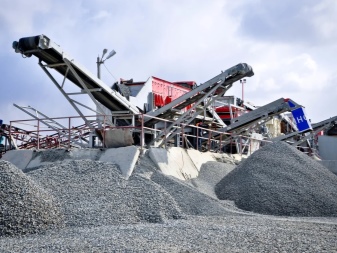
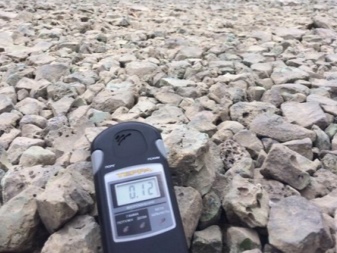
Extraktionsfunktionen
In der Umgangssprache wird normalerweise ein Ausdruck wie "Schotterbergbau" verwendet - dies ist nicht ganz richtig, tatsächlich wird Schotter durch eine künstliche Methode gewonnen. Es wird nur Gestein abgebaut - das ist der Ausgangsrohstoff. Das Material selbst wird mit Brech- und Siebanlagen hergestellt.
Der Prozess selbst besteht aus drei Stufen - dies ist die Gewinnung des Ausgangsmaterials, Zerkleinerung, Sortierung.
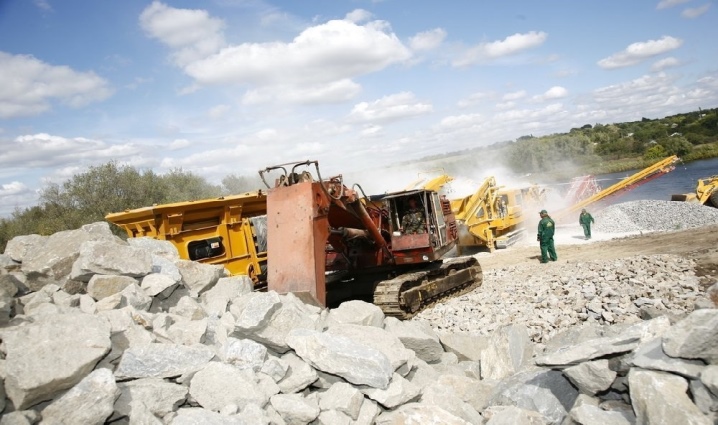
Rassenextraktion
Schotterproduzenten verwenden unterschiedliche Rohstoffe - Granit, Marmor, Kalkstein usw., je nachdem, welches Produkt Sie am Ende erhalten möchten. Granitschotter wird aus jahrhundertealtem vulkanischem (vulkanischem) Material - gefrorenem Magma - hergestellt. Vor Arbeitsbeginn wird ein Steinbruch vorbereitet - die oberste Rasenschicht mit Gras wird entfernt, dann die oberste Erdschicht. Granitblöcke werden durch Explosionen und Technologie aus dem Boden gehoben, bei Bedarf werden sie in kleinere Stücke zerteilt.
Die Herstellung von Schotter kann gezielt oder als Nebenprodukt erfolgen. Bei der ersten Herstellung wird das Material von höherer Qualität und Preis sein. Im zweiten Fall ist Schotter ein Nebenprodukt, das bei der Gewinnung von Mineralien oder bei der Herstellung von Produkten anfällt. Die Gewinnung von Gestein kann auf vier Arten durchgeführt werden.
- Steinschneiden - diese Methode ist die teuerste, aber gleichzeitig eine der effektivsten. Mit Hilfe von Steinschneidegeräten werden große Blöcke sofort im Steinbruch abgesägt. Die Maschinen sind mit Seilsägen oder Scheibensägen mit Diamantspitzen ausgestattet. Bei dieser Arbeitsweise erhält man Klumpen der gewünschten Form und Größe, es bilden sich keine Mikrorisse.
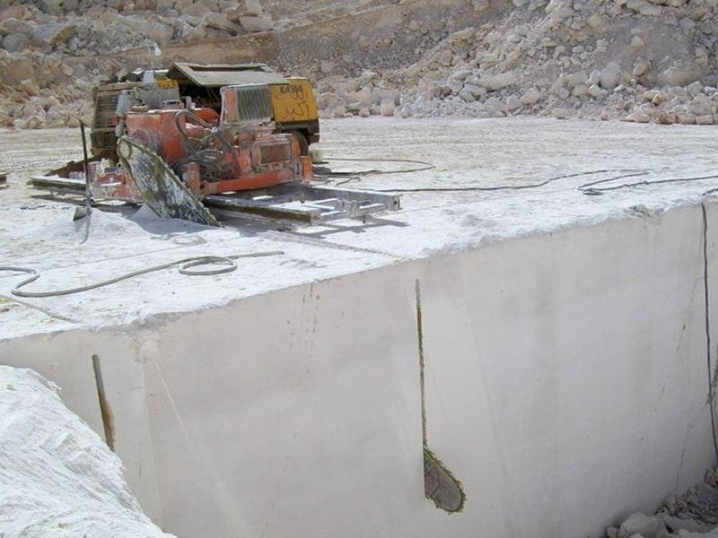
- Buroklinova - Diese Methode ist eine der ältesten und wird jetzt nur noch selten verwendet.Hier beginnt die Arbeit mit dem Umriss des Blocks, dann werden entlang dieser Markierung Brunnen gebohrt. Darin werden spezielle Stifte eingelegt, bei denen der Block entlang einer vorbestimmten Linie getrennt wird. Mit dieser Methode werden in der Regel die härtesten Gesteine abgebaut. Der einzige Nachteil dieser Technologie ist, dass sie nur für kleine Gesteinsbrocken geeignet ist.
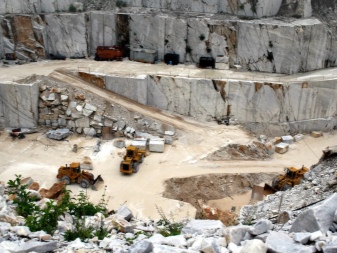
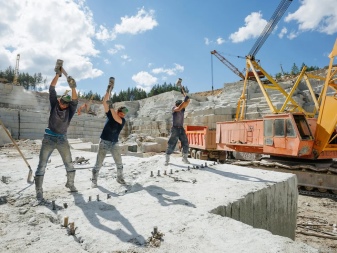
- Bürohydrokline Ist eine fortschrittliche Borokline-Technologie. Der Abbau verläuft nach einem identischen Plan, jedoch ersetzen Stahlkeile die hydraulischen Keile. Sie sind mit Wasser gefüllt, das unter Druck steht, und dehnen sich in den Bohrlöchern sanft aus. Diese Methode kann verwendet werden, um sehr große Steinstücke an den unzugänglichsten Stellen zu extrahieren. Ein großer Vorteil der braunen Hydro-Wedge-Technologie ist die völlige Geräusch- und Vibrationsfreiheit, damit die Gesteinsstruktur weitestgehend erhalten bleibt.
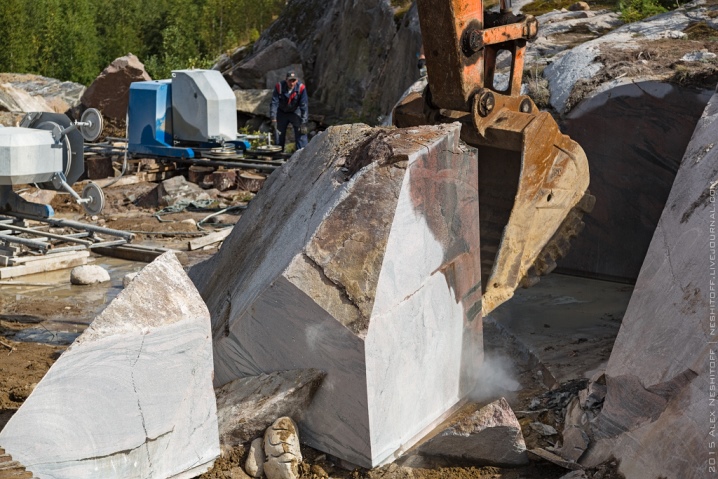
- Bohren und Sprengen (explosiv) - Diese Methode ist sowohl bei der Gewinnung von Gestein als auch bei der Gewinnung von Erzen am beliebtesten. Außerdem werden Löcher in den Stein gebohrt und Sprengstoff hineingelegt. Die Explosion bricht viele Steine ab, die größten werden gesammelt und zur Verarbeitung abtransportiert.
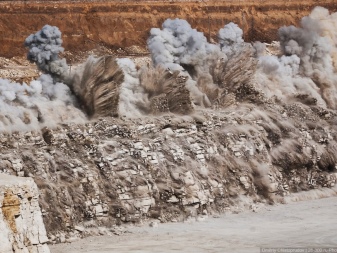
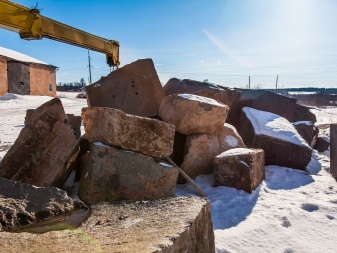
Diese Methode erfordert eine höhere Genauigkeit der Berechnungen, jeder Fehler führt zu einer Erhöhung der Kosten. Eine große Menge Sprengstoff verdirbt den Fels, bei einem Mangel an Sprengstoff werden die Stücke im Gegenteil zu groß, sie müssen wieder gespalten werden.
Das Bohr- und Sprengverfahren ist das wirtschaftlichste und zugleich destruktivste, da bei einer Explosion nur 70 % des Gesteins für die Weiterverarbeitung geeignet bleiben, während die restlichen 30 % der Siebung zugeführt werden.
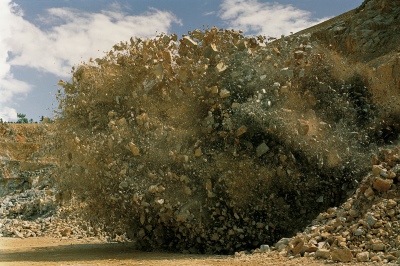
Sich trennen
Dann werden Steinstücke auf Lastwagen verladen und zu Verarbeitungspunkten in Bunkern gebracht. Von ihnen wird das Material zu den Feedern geschickt (spezielle Geräte, dank denen die Rohstoffversorgung gleichmäßig erfolgt). Die Anfangsabmessungen der Steine reichen 50 - 120 Zentimeter und die Größe des fertigen Produkts sollte 0,5 - 12 Zentimeter betragen. Beim Zerkleinern können Stücke hunderte Male zerkleinert werden, so dass die Arbeit normalerweise in 2 - 4 Stufen erfolgt.
Das Zerkleinern kann auf drei Arten erfolgen - groß (bis zu 30 cm), mittel (bis zu 10 cm), fein (bis zu 4 cm). In modern ausgestatteten Fabriken findet der Zerkleinerungsprozess gleichzeitig mit der Sortierung statt. In jeder Phase wird das Gestein einer Vorsortierung unterzogen, bei der größere Steine von kleinen getrennt werden.
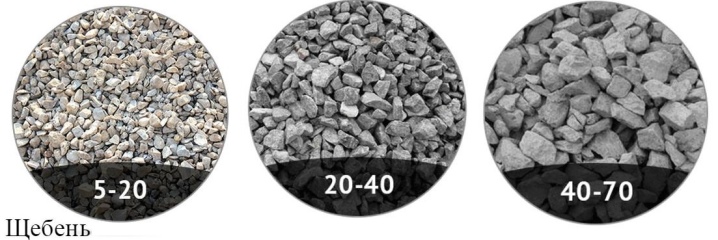
Somit werden nur die Steine, die zerkleinert werden müssen, weiter in die Anlage geleitet.
Um mit Schotter zu arbeiten, werden 6 Arten von Zerkleinerungsgeräten verwendet.
- Kiefer - wird in der ersten Zerkleinerungsstufe verwendet. Ihr Wirkprinzip ist die stoßfreie Zerkleinerung. Zur Ausstattung gehören zwei Platten (Wangen), zwischen die Granitstücke gelegt werden. Dann beginnen sie, sich einander zu nähern, wodurch Steine bröckeln.
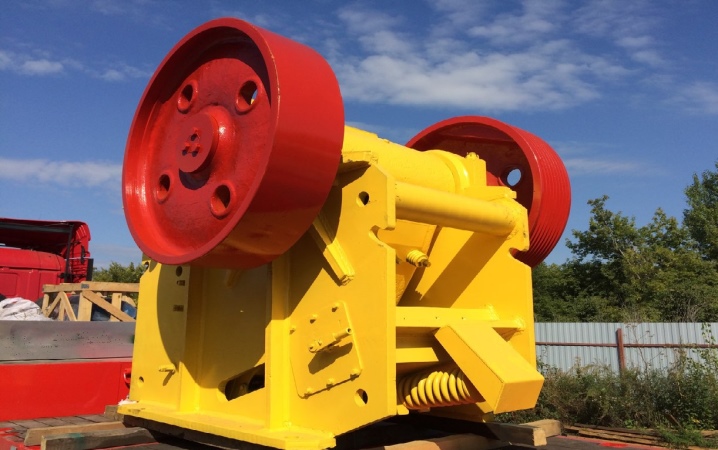
- Roller - die Arbeit erfolgt nach dem gleichen System, wie bei Backenbrechern, nur werden hier anstelle von Platten spezielle Wellen gebaut, die sich in verschiedene Richtungen drehen. Die Oberfläche der Wellen kann glatt, gezahnt oder genutet sein.
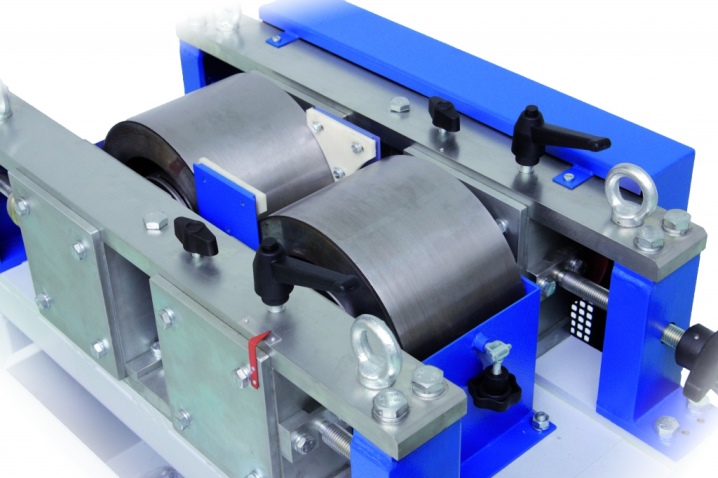
- Konisch - zum Schleifen von Granit in kleinen und mittleren Abmessungen. Die Konstruktion solcher Brecher ist komplizierter - in einem stationären konischen Behälter befindet sich ein beweglicher Kegel, dessen Oberseite nach oben gerichtet ist. Durch einen speziellen Trichter werden die Steine in das Dickicht eingebracht und der Kegel bewegt sich hin und her, nähert sich dem feststehenden Boden und zerkleinert so das Gestein.
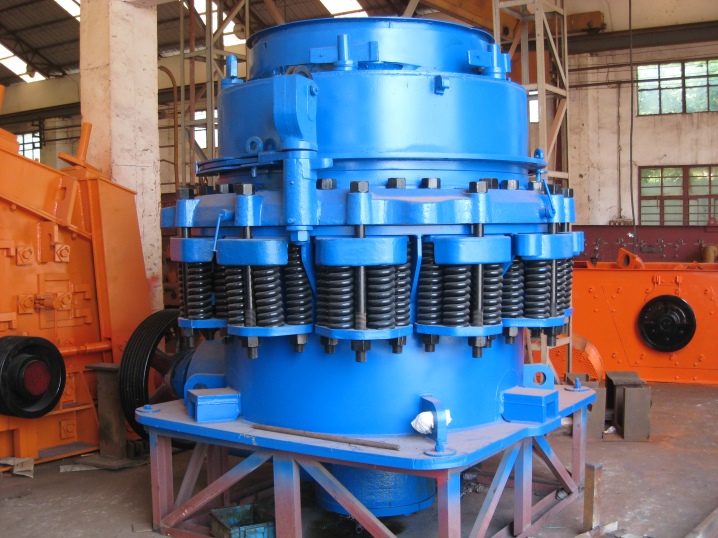
- Rotary - das Funktionsprinzip dieser Brecher ist der Schlag. Das Gerät sieht aus wie eine Kammer, an deren Rändern sich Prallbleche befinden, und in der Mitte befindet sich ein Rotor. An ihm sind Schlägel (Schulterblätter) befestigt. In die Brechmaschine eintretender Granit schneidet in die Prallplatten und ineinander. Der Betrieb von Rotationsgeräten zeichnet sich durch eine hohe Selektivität aus - das heißt, die Mehrheit der Granitsteine ist würfelförmig (80 - 85%).
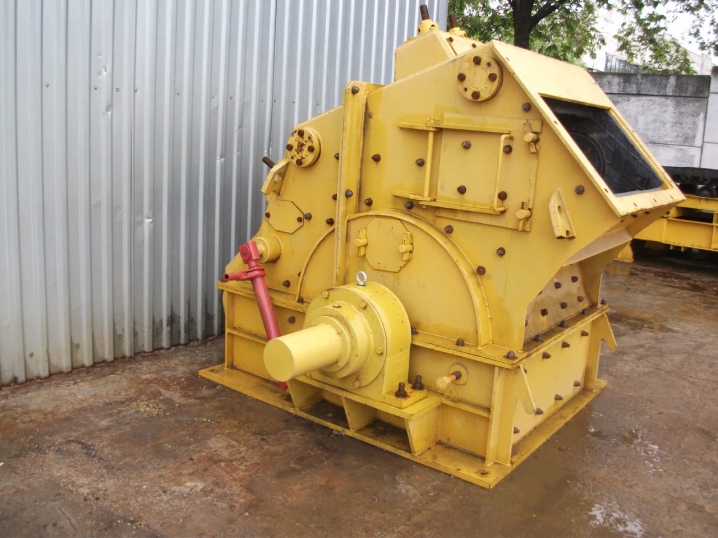
- Hammerbrecher - das Design solcher Brecher ist identisch mit dem vorherigen Typ, aber statt Klingen funktionieren hier Hämmer. Am häufigsten werden diese Brecher für weiches Gestein eingesetzt.
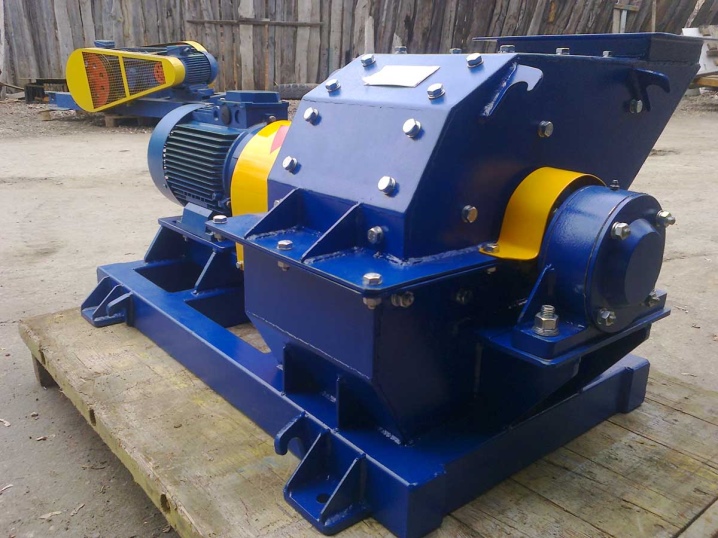
- Zentrifugal – der Brecher ist eine Zentrifuge, bei dem der Fels mit hoher Geschwindigkeit gegen seine Wände und gegeneinander prallt. Dieses Gerät darf mit Granit bis zu 10 Zentimeter arbeiten.
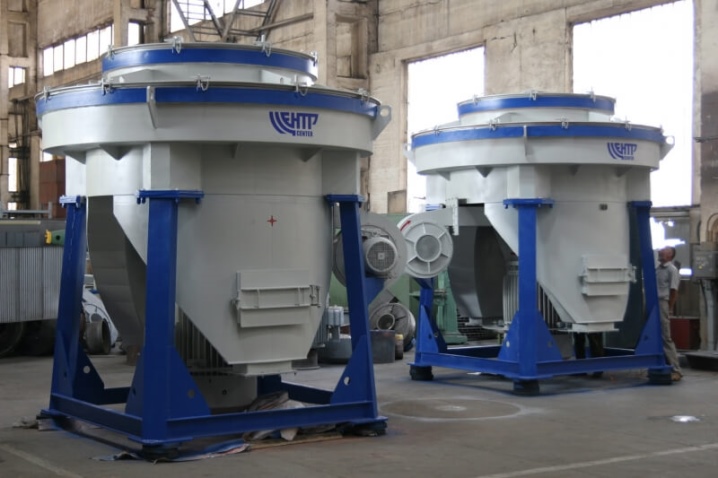
Sortierung
Nachdem das Gestein die Brechstufe passiert hat, gelangt es in die Siebschwingsiebe - Siebe. Sie erhielten einen solchen Namen für das charakteristische Geräusch während des Betriebs. Sortieren kann so sein.
- Vorläufig - hier werden Steine, die nicht zerkleinert werden müssen, getrennt und minderwertig vor dem Zerkleinerungsprozess durchgeführt.
- Kontrolle - wird nach dem Zerkleinern durchgeführt. Dabei wird Granit abgetrennt, der einer erneuten Bearbeitung bedarf.
- Commodity - Bei dieser Art der Sortierung passiert Schotter, bevor er für den Verkauf vorbereitet wird.
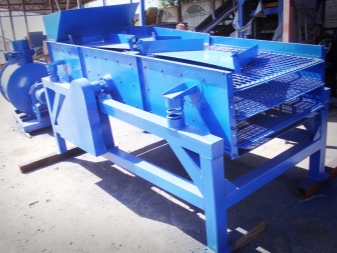
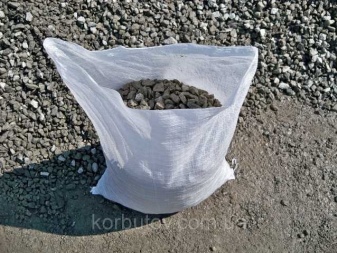
Hauptmerkmale
- Flockigkeit - der Grad der Granitebene, die Eigenschaft wird durch das Vorhandensein von Einschlüssen in Form von Nadeln und Platten in der Gesteinsstruktur bestimmt. Die Haftung an verschiedenen Stoffen hängt von der Form des Schotters ab. Ein niedrigerer Flockigkeitskoeffizient weist auf eine hohe Granitqualität hin.
- Stärke - das Merkmal wird bei der Errichtung von Gesamtgebäuden berücksichtigt. Wenn Schotter komprimiert wird, zeigt sich seine ultimative Festigkeit. Nach den Standards des aktuellen GOST sollte der Prozentsatz an Steinen mit einer Mindestfestigkeit nicht höher als 5 Einheiten sein.
- Schüttdichte - Das Merkmal bestimmt das spezifische Gewicht von 1 m3 im natürlichen Zustand, dh die Hohlräume und Poren zwischen den Stücken werden berücksichtigt. Wie viel das Material wiegt, hängt direkt davon ab. Um herauszufinden, wie viele Tonnen Schotter in einem Würfel sind, müssen Sie 1 Tonne (1000 kg) durch den Schüttdichtekoeffizienten teilen. Viele Hersteller verpacken Schotter in Säcke mit 25, 30, 35, 40, 42, 45, 50, 55, 60 Litern. Um herauszufinden, wie viele Schuttsäcke sich in einem Würfel befinden, können Sie spezielle Tabellen verwenden. Diese Eigenschaft bestimmt, wie die Produkte gelagert und transportiert werden und wie viel Zementmischung während des Baus benötigt wird. Je höher der Dichtekoeffizient, desto weniger Mörtel wird benötigt.
- Frostbeständigkeit - Die Eigenschaft kennzeichnet, wie viele Auftauen und Gefrieren der Schotter aushält. Es ist mit dem Buchstaben "F" gekennzeichnet und die Zahl daneben gibt die Anzahl der Einfrier- / Auftauwiederholungen an - F15, 25, 50, 100, 150, 200, 300, 400.
- Radioaktivität - bei der Auswahl eines Produktlieferanten berücksichtigt werden. Schotter ist eine Strahlungsquelle und kann sie zusätzlich ansammeln. Schotter wird in 3 Kategorien unterteilt: 1 - weniger als 370 Bq / kg - für den Bau von Wohn- und Nichtwohngebäuden; 2 - 370 - 740 Bq / kg - für Straßenbetten und Fundamente von Fabriken; 3 - mehr als 740 Bq / kg - nur für Autobahnen zulässig.
- Adhäsion - Dies ist ein Indikator dafür, wie fest der Schotter an verschiedenen Substanzen haftet. Die höchste Haftung der Rasse ist grau.
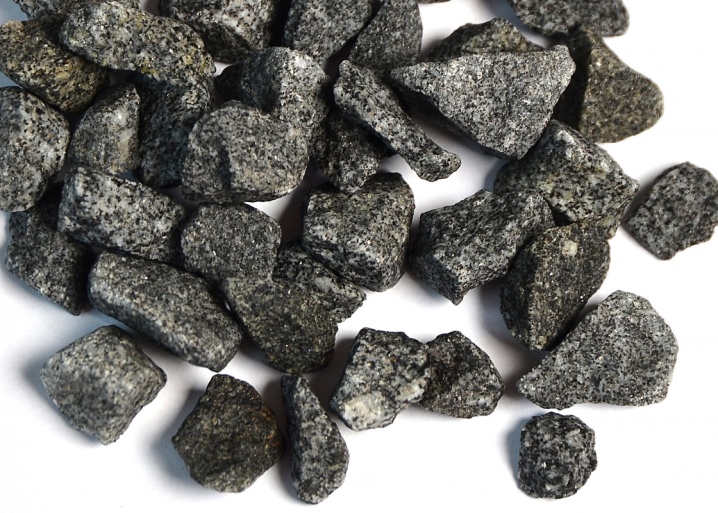
Typen und Marken
Insgesamt gibt es fünf Sorten.
- М1200 - 1400 - hohe Festigkeit.
- М800 - 1200 - strapazierfähiger Schotter.
- М600 - 800 - mittelstark.
- М300 - 600 - schwache Stärke.
- M200 - sehr schwache Stärke.
Der Farbton des Granits hängt von dem Gebiet ab, in dem das vulkanische Material abgebaut wurde. Es kann weiß, grau, rosa, rot usw. sein.
Die Farbpalette wird durch die Fülle an Einschlüssen in der Struktur des Granitsteins bestimmt.
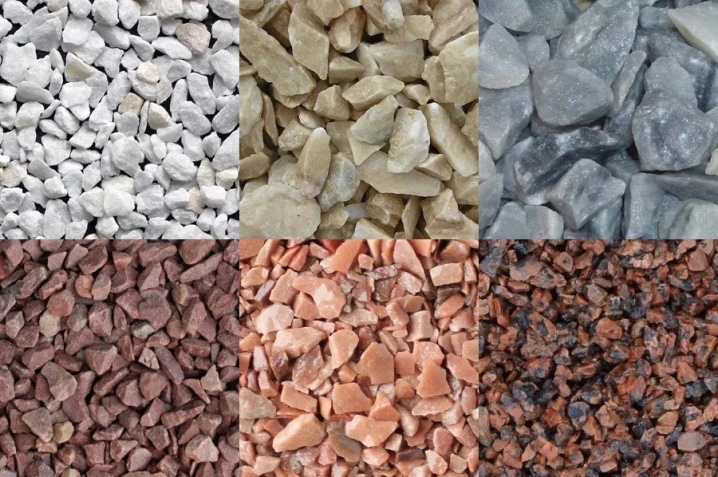
In Fabriken wird Schotter einer zusätzlichen Verarbeitung unterzogen.
- Spülen - ist notwendig, um das Material von Staub und Lehm zu reinigen. Ein Spülbedarf entsteht erst, wenn der zulässige Anteil an Ton- und Staubpartikeln überschritten wird. Der Waschvorgang ist recht aufwendig und teuer, außerdem ist eine zusätzliche Trocknung des Produkts erforderlich. Gewaschener Schotter wird selten und nur für bestimmte Zwecke hergestellt.
- Bitumenimprägnierung - Schotter mit dieser Behandlung wird im Straßenbau verwendet, er wird mit Teer, Bitumen oder Bitumenmörtel bedeckt. Der Prozess findet in Asphaltmischanlagen statt.Bituminöser oder schwarzer Schotter kann nicht lange gelagert werden, da seine Nutzungsdauer kurz ist, wird er normalerweise sofort auf die Baustelle geschickt.
- Färberei - diese Verarbeitung dient nur dekorativen Zwecken. Granit kann in Fabriken oder zu Hause gebeizt werden. Farbiger Schotter wird nur nach vorheriger Bestellung und in Kleinserien hergestellt. In diesem Fall ist zu beachten, dass selbst die hochwertigsten Farbstoffe mit der Zeit verblassen oder abplatzen.
- Schleifen (Taumeln) - solcher Granit wird auch in dekorativen Arbeiten verwendet. Getrommelter Schotter ist ein Material, das mechanisch belastet wurde, wodurch scharfe Kanten geglättet werden. Die Verarbeitung erfolgt in einer Taumeltrommel, in die Naturstein, abrasive Stoffe und Wasser eingebracht werden. Durch Reibung gegeneinander und gegen Schleifmittel findet der Schleifvorgang statt.
Das Trommeln ist ein ziemlich kostspieliger Prozess, daher wird polierter Schotter nur nach vorheriger Bestellung hergestellt.
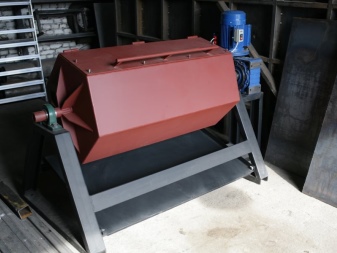
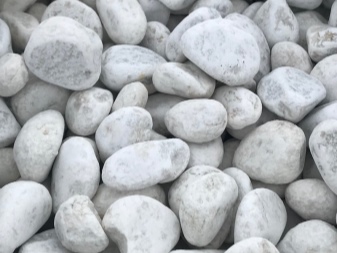
Fraktionsübersicht
Eine der wichtigsten Eigenschaften von Schotter ist seine Fraktionierung, die bei der Extraktion und dann bei der Verarbeitung von Granit zugewiesen wird. Unterteilt in Kategorien.
- Von 0 bis 10 mm - ShchPS (Schotter-Sand-Gemisch), die Zusammensetzung enthält Komponenten wie Sand und Schotter. Laut GOST haben die Produkte eine eigene granulometrische Klassifizierung bzw. gibt es mehrere Arten von Sand-Schotter-Gemischen. Hervorragend als Drainageschicht, zum Asphaltieren von Straßen.
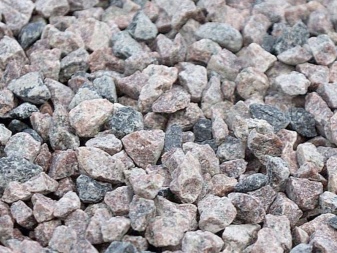
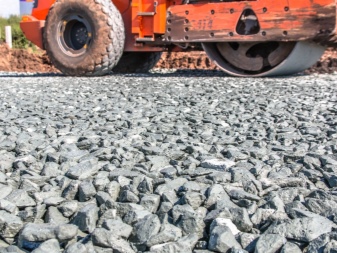
- Von 5 bis 10 mm - feiner Granit. Die Produkte zeichnen sich durch ihre Langlebigkeit und günstige Preisklasse aus. Es wird zur Herstellung von Betonzusammensetzungen verwendet, die bei der Arbeit mit massiven und schweren Gegenständen verwendet werden.
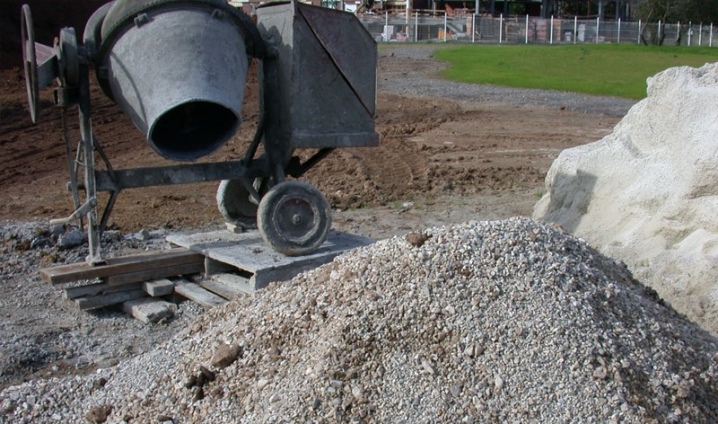
- 5 bis 20 mm sind zwei miteinander vermischte Größenklassen. Ideal für die Fundamentierung von Häusern.
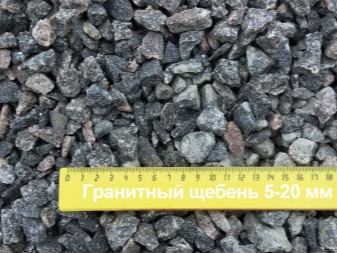
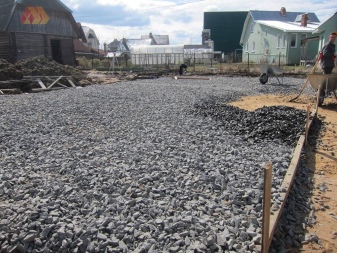
- 20 bis 40 mm - Mittlerer Granit, das Material fand seinen Zweck beim Füllen von Fundamenten von Wohngebäuden, Fabrikgelände, Asphaltierung, Verlegung von Straßenbahnlinien.
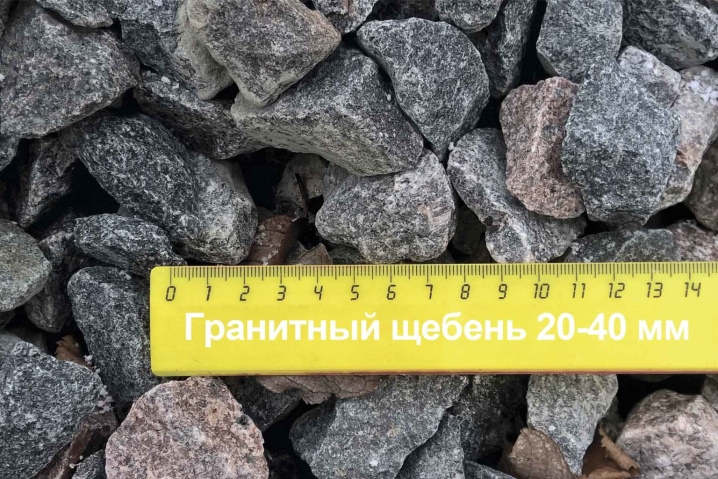
- Von 40 bis 70 mm - hochfeste großformatige Granitsteine. Sie werden auf Baustellen von Großobjekten eingesetzt.
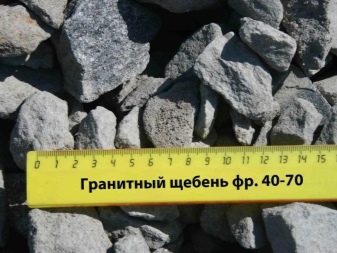
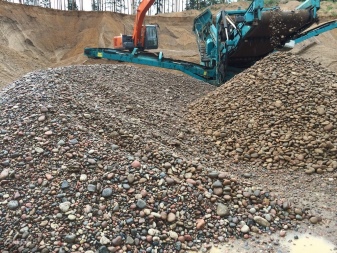
- 70 bis 120 mm, 150 bis 300 mm - Granit von großer Standardgröße mit unregelmäßiger Form. GOST für diese Kategorie ist in speziellen Tabellen aufgeführt, die beim Bau von Brücken und Dämmen verwendet werden. Aufgrund seiner erhöhten Festigkeit wird es beim Verlegen von Trümmerbetonuntergründen verwendet.
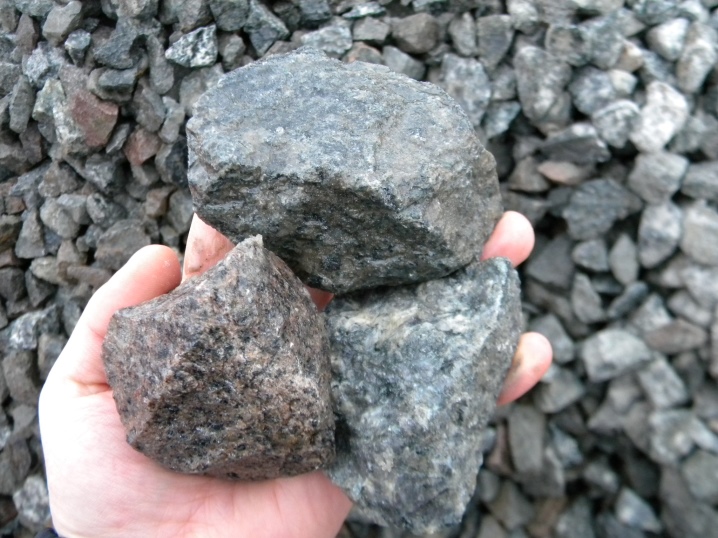
Aussteigen
Fraktion von 0 bis 5 mm oder Granitspäne - diese Kategorie ist die kleinste, sie tritt als Sekundär- oder Nebenmaterial auf. Das Rechengut sieht aus wie Sand, hat aber die Eigenschaften von Granit.
Es wird bei der Anordnung von Fußgängerwegen, Gehwegen und Parkanlagen verwendet.
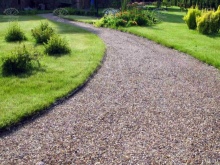
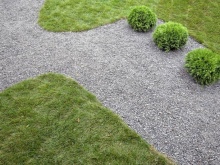
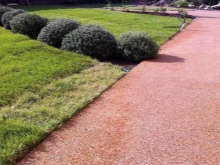
Anwendungen
- Im Bauwesen - zum Herstellen von Beton, einer Drainageschicht, zum Aufteilen in kleinere Größen, zur Verstärkung des Bodens unter den Fundamenten von Gebäuden, zum Nivellieren von Grundstücken und Standorten.
- Im Straßenbau - für Schmutz, Asphalt und Eisenbahnen.
- Bodenverbesserung - für Wege und Wege, Einfahrt in das Territorium, Bodenverdichtung, Deponierung von Parkplätzen und Sportplätzen, Schutz vor Eis und Eis.
- Für die Landschaftsgestaltung - Dekoration von Blumenbeeten, Bächen, künstlichen Gewässern, Gabionen und Alpenrutschen.
- In der Produktion - für Pflastersteine und Stahlbetonprodukte, mineralische Schüttgüter.
- Ingenieurarbeiten - für Brücken, Dämme und Dämme, Überführungen.
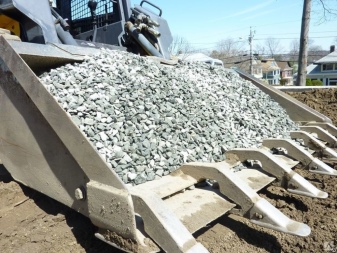
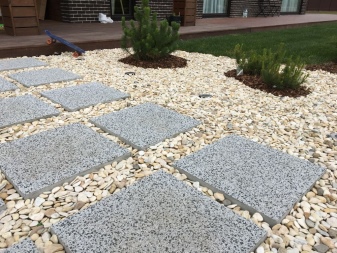
Der Kommentar wurde erfolgreich gesendet.