Alles über Maschinengewindebohrer
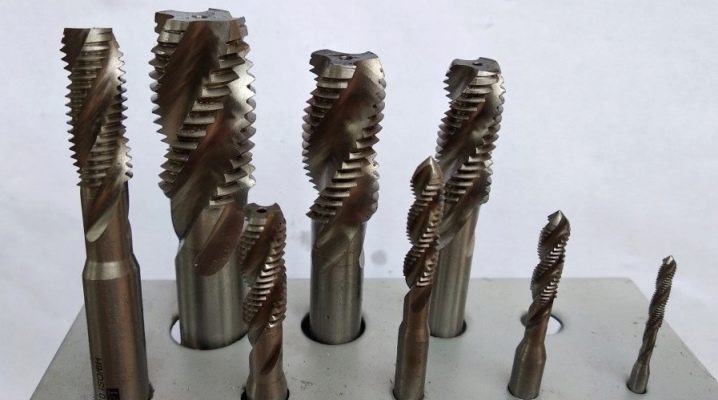
Um viele Branchen und Werkstätten zu organisieren, müssen Sie alles über Maschinengewindebohrer wissen, über die Anforderungen an sie nach GOST, über verlängerte, komplette und mit einer Schraube versehene Nutkonstruktionen. Es ist hilfreich zu verstehen, was M6 und M8, M10 und M12, M4 und M3, M5 und andere Gewindebohrergrößen bedeuten. Und Sie müssen sich auch mit den Nuancen der Auswahl und praktischen Anwendung solcher Modelle vertraut machen.
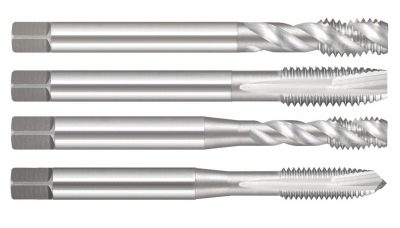
Design-Merkmale
Die Hauptbesonderheit jedes Maschinengewindebohrers wird durch seinen Namen erklärt. Dieses Gerät ist ausschließlich für den Einsatz in verschiedenen Maschinen und Geräten bestimmt. Es unterscheidet sich von manuellen und maschinell-manuellen Optionen durch seine einzigartige Geometrie. Die Form wird aus einem bestimmten Grund geändert - sie ist darauf ausgelegt, die höchstmöglichen Geschwindigkeiten bei der Verarbeitung zu erreichen. Drehvorrichtungen werden gezielt für den Einbau in die Zentren des entsprechenden Maschinentyps geschaffen; der einzige Unterschied liegt im Design des Heckteils.
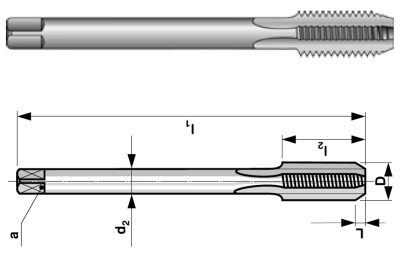
Das Ansaugsegment für Durchgangskanäle beträgt 5 oder 6 Umdrehungen. Um ein Sackloch zu schneiden, reichen sogar 2 Umdrehungen. Dieser Umstand wird von Designern aktiv genutzt, um die Länge ihrer Entwürfe auf ein vertretbares Maß zu reduzieren.
Das Heckteil kann in einem Balken- oder Quadratformat hergestellt werden. Die Struktur der Nut bestimmt, wie effizient das Gewinde geschnitten wird und wie gut die Späne entfernt werden.
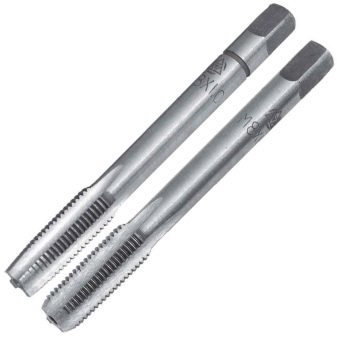
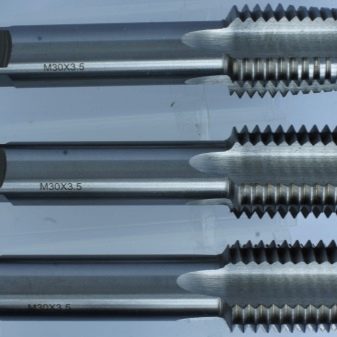
Am beliebtesten sind Wasserhähne mit 3 oder 5 Flöten. Der Spanwinkel des Produkts ist wichtig. Am allerwenigsten - von 0 bis 5 Grad - sollte es für die Arbeit mit Gusseisen sein. Um Stahl zu bearbeiten, benötigt man Werte zwischen 5 und 10 Grad. Manipulationen mit Buntmetallen und darauf basierenden Legierungen sind am einfachsten mit einem Frontwinkel von mindestens 10 und höchstens 25 Grad durchzuführen.
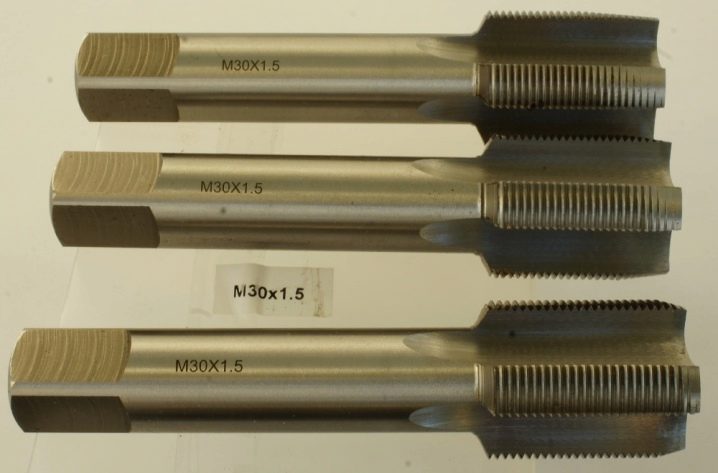
Die hinteren Winkel reichen von 4 bis 12 Grad. Meist verlaufen die Rillen gerade. Wenn jedoch eine optimale Spanabfuhr kritisch ist, sollte die Neigung zwischen 8 und 15 Grad betragen. Langschaftmodelle sind normalerweise für metrische Nuten von M3 bis einschließlich M10 ausgelegt. Der Standard für ihre Entwicklung und Produktion wird durch direkte Übersetzung der globalen Norm ISO 8051-89 erhalten.
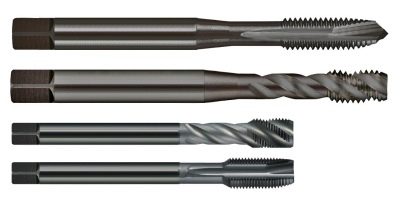
Komplettversionen sind standardmäßig auch für metrische Gewinde ausgelegt. Sowohl komplette als auch einzelne Gewindebohrer können für Durchgangs- und Sacklöcher ausgelegt werden. In einigen Fällen hat der Striper einen langen Schaft, was für ernsthafte Arbeiten sehr praktisch und bequem ist. Produkte mit spiralförmiger Nut müssen alle die Anforderungen erfüllen GOST 17933-72, die ihre Relevanz behält.
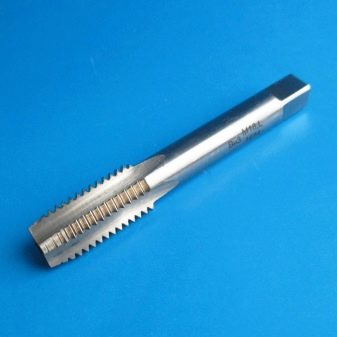
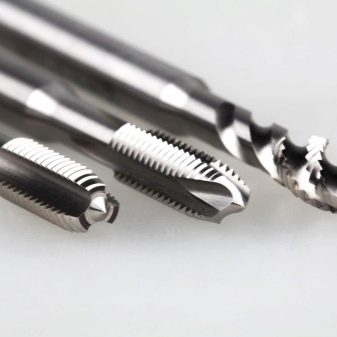
Die Norm spezifiziert:
-
Ausrichtung der Rillen selbst;
-
Neigungswinkel für verschiedene Fälle;
-
Abmessungen der Quadrate;
-
Grundmaßtoleranzen;
-
Nenngewindequerschnitte.
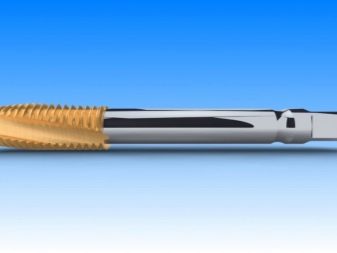
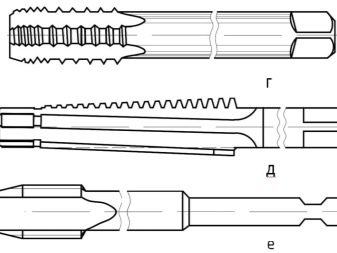
Abmessungen (Bearbeiten)
Diese Werte werden gemäß GOST 3266-81 eingestellt. Ein Produkt der Kategorie M3 hat eine Hauptschneidteilung von 0,5 mm. Gleichzeitig kann es ein 5-mal größeres Loch stanzen - bis zu 0,25 cm Ich muss sagen, dass solche Proportionen nicht immer eingehalten werden. So bereiten Gewindebohrer vom Typ M4 mit einer Gewindesteigung von 0,7 mm Löcher mit einer Größe von 0,37 cm vor (Koeffizient 5,28). Für M5 beträgt das Verhältnis 0,08 und 0,42 cm (Koeffizient 5,25).
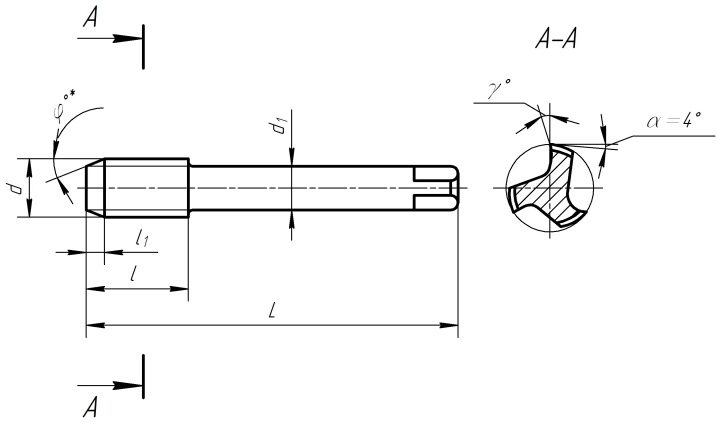
Andere Größen (cm):
-
M6 - 0,1 und 0,495;
-
M7 - 0,1 und 0,595;
-
M8 - 0,125 und 0,67;
-
M9 - 0,125 und 0,77;
-
M10 - 0,15 und 0,843;
-
M11 0,15 und 0,943;
-
M12 - 0,175 und 1,02;
-
M16 - 0,2 und 1,39;
-
M20 - 0,25 und 1,735;
-
M30 - 0,35 und 2,63.
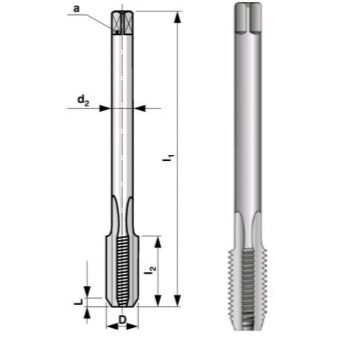

Auswahlkriterien
Zunächst müssen Sie klären, welche Art von Metall Sie bearbeiten müssen. Einige Eigenschaften von Gewindebohrern für verschiedene Metallarten wurden oben beschrieben, und es macht keinen Sinn, darauf zurückzukommen. Aber auch andere Punkte sind eine Überlegung wert. Dabei ist die Anzahl der Rillen zu berücksichtigen, durch die die Späne austreten und die Spezialflüssigkeit eintritt. Diese Anzahl kann 2 bis 6 Stück betragen und wird nach sorgfältiger technischer Analyse ausgewählt.
Es lohnt sich, sowohl die Profile der Täler als auch die Richtung des Rillenlaufs zu analysieren. In typischen Universalgewindebohrern werden überwiegend gerade Nuten verwendet.

Die linke Richtung der Helix ermöglicht es Ihnen, ein "Durch"-Gewinde zu machen. In diesem Fall werden die Späne vor dem Gewindebohrer selbst gruppiert und der Schnitt verschlechtert sich nicht. Bei Blindkanälen wird die rechte Position der Rillen empfohlen; Bei dieser Option werden die Späne zurückgezogen und nicht komprimiert (wenn sie gequetscht würden, würde das Werkzeug sehr leicht verschleißen).
Der Ansaugblock hat die Form eines Kegels. Dadurch kann das Eindringen der Zähne in das hartnäckigste Material deutlich erleichtert werden. Die Neigungswinkel können 3-20 Grad betragen. Sie werden dadurch bestimmt, ob der Gewindebohrer ein Primär- oder ein Schlichtgewinde einfügt. Es ist auch notwendig, das Kalibrierteil zu bewerten, das die Reibungskraft reduzieren soll.
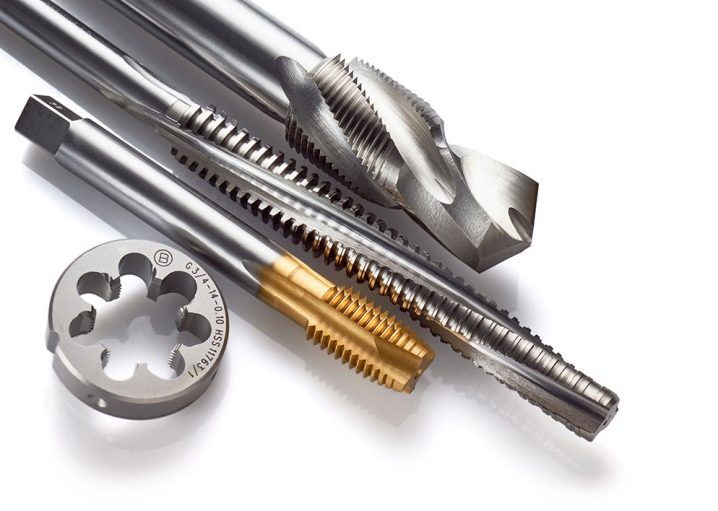
Einige Gewindebohrer haben kurze Flöten oder gar keine Flöten. Solche Vorrichtungen eignen sich gut zum Herstellen von Fäden in einer Aluminiumlegierung verschiedener Zusammensetzungen. Sie sind auch für zähe Stähle mit niedrigem Kohlenstoffgehalt geeignet. Aber auch für besonders feste Stähle mit hohem Anteil an Legierungszusätzen ist dieses Gerät sinnvoll. Die spiralförmigen Spannuten ermöglichen den erfolgreichen Einsatz des Gewindebohrers als Bestandteil eines Bearbeitungszentrums, wodurch hervorragende Blindgewinde hergestellt werden.
Bei einigen Modellen sind die Zähne versetzt angeordnet. Das bedeutet, dass sie in der Schlichtepartie nacheinander abgeschert werden. Bei diesem Ansatz ist die Reibung geringer.
Dadurch wird die Handhabung viskoser Materialien vereinfacht. Stufengewindebohrer kommen zum Einsatz, wenn es notwendig ist, einzelne Zonen mit einem speziellen Formgebungsschema zu bearbeiten.
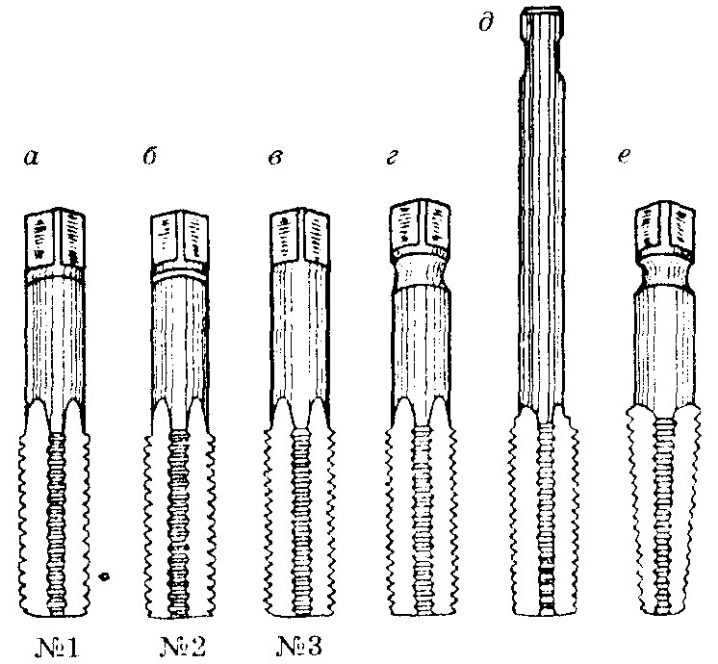
Kombinierte Markiergeräte haben einen Bohrschritt oder einfacher einen konventionellen Bohrer. Räumgewindebohrer werden zum Schneiden von Gewinden mit beliebigem Querschnitt und Steigung auf Drehmaschinen verwendet. Wenn es an modernen Werkzeugmaschinen um maximale Produktivität geht, kommen Gewindebohrer mit Innenkanal zur Zuführung einer Schmier- und Kühlflüssigkeit zum Einsatz. Sie sind sowohl für Universal- als auch für Spezialwerkzeugmaschinen geeignet.
Manchmal besteht die Aufgabe darin, einen besonders großen Durchgangsfaden (von 5 bis 40 cm) vorzubereiten. In solchen Fällen sind Klingelhähne erforderlich. Es ist ein Montagewerkzeug, das in separate Schneidsegmente unterteilt ist. Auch Kühlflüssigkeit strömt in das Gehäuse ein. Bietet 16 Arbeitsstifte; Auch die Aufnahme großer Spänemengen ist eine sinnvolle Option.

Nach der Art des gebildeten Gewindes gibt es neben den traditionellen metrischen auch:
-
Zoll;
-
konisches Rohr;
-
zylindrische Wasserhähne.
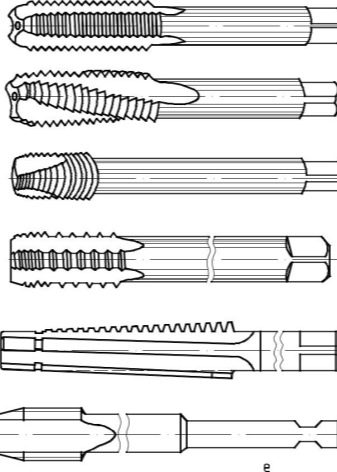
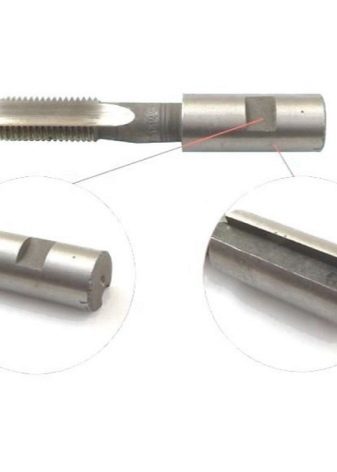
Maschinenlinienmarkierer arbeiten mit hohen Geschwindigkeiten. Daher werden sie sehr heiß. Dadurch ist ein normaler Betrieb nur bei Verwendung hochwertiger Schnellarbeitsstähle gewährleistet. Unter diesen ist die am meisten bevorzugte Legierung P18. Bei etwas geringeren Belastungen können Sie auch P6M5 oder P6M5K5 (K8) verwenden; Die Maschinen mit der höchsten Produktivität sind immer mit Hartmetallwerkzeugen ausgestattet.
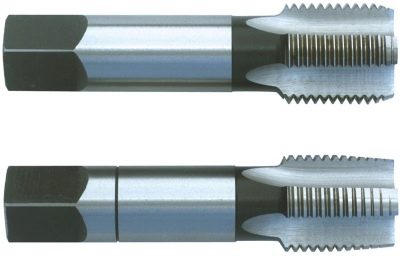
Anwendung
Selbst viele Nicht-Spezialisten wissen, dass der Gewindebohrer zum Gewindeschneiden dient. Aber hier gibt es einige Feinheiten. Für einen ordnungsgemäßen Betrieb müssen Sie den Querschnitt des Lochs genau bestimmen - dies ist am einfachsten unter Bezugnahme auf die technischen Normen zu bewerkstelligen. Der wichtigste Schritt bei der Gewindevorbereitung ist das Bohren eines Lochs mit dem erforderlichen Querschnitt.Fehler in dieser Phase führen entweder zu einem ungenügend festen Gewinde oder zum Bruch eines überlasteten Werkzeugs.
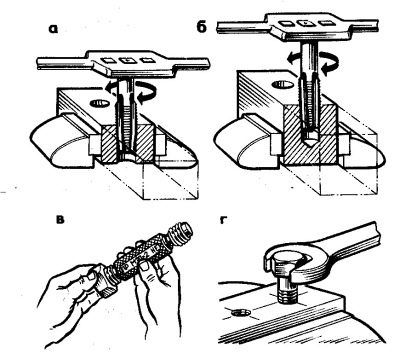
Meistens ist die Arbeit in zwei Phasen unterteilt. Zuerst werden die Nuten mit einem groben Gewindebohrer geformt. Anschließend werden sie mit einem Schlichtwerkzeug finalisiert. Soll das Gewinde in einem tiefen Kanal geformt werden, wird der Vorgang periodisch unterbrochen, um die Späne zu beseitigen. Und auch in solchen Fällen können Sie nicht auf Schmierung verzichten.
Viele Leute empfehlen die Verwendung spezieller Emulsionen. Aber auch die Verwendung von Kerosin oder Leinöl kann eine gute Option sein.
Beim Verlegen von Blindkanälen muss deren Tiefe größer als die Länge des geschnittenen Segments sein. Wenn der Gewindebohrer während des Betriebs nicht über die erforderliche Gewindelänge hinausgeht, ist er unvollständig. Die Nuten selbst entstehen nur, wenn das Werkstück in einen Schraubstock eingespannt wird.
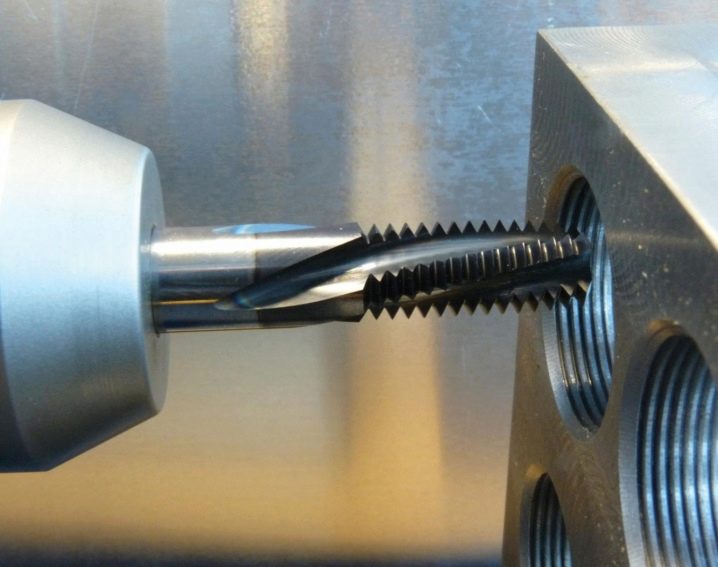
Die richtige Auswahl des Kühlschmierstoffs für eine bestimmte Anwendung ist sehr wichtig. Bei der Bearbeitung von Messing- und Stahlknüppeln wird Leinöl verwendet. Eine verdünnte Emulsion ist relativ vielseitig. Für Gusseisen- und Bronzekonstruktionen ist Trockenlauf zulässig. Wenn Sie Gewinde an Aluminiumteilen herstellen müssen, müssen Sie Kerosin verwenden; Maschinenöl und andere Mineralöle sollten nicht verwendet werden.
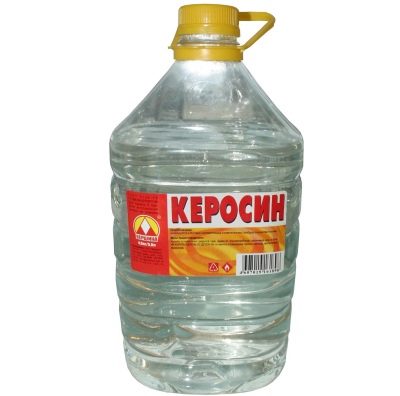
Das regelmäßige Entfernen des Kanalreinigungswerkzeugs ist nützlich, wenn an harten und weichen Metallen gearbeitet wird. Diese Regel muss beachtet werden, auch wenn das Loch selbst dort flach ist. Es ist unbedingt erforderlich, die Richtigkeit des Einsetzens des Werkzeugs und das Fehlen von Verzerrungen zu überprüfen. Die kritischsten in dieser Hinsicht sind Blindkerben mit geringer Tiefe. Die Arbeitsgeschwindigkeit wird unter Berücksichtigung der Materialart und der resultierenden Belastungen ausgewählt; Das Futter sollte gleichmäßig und glatt sein.
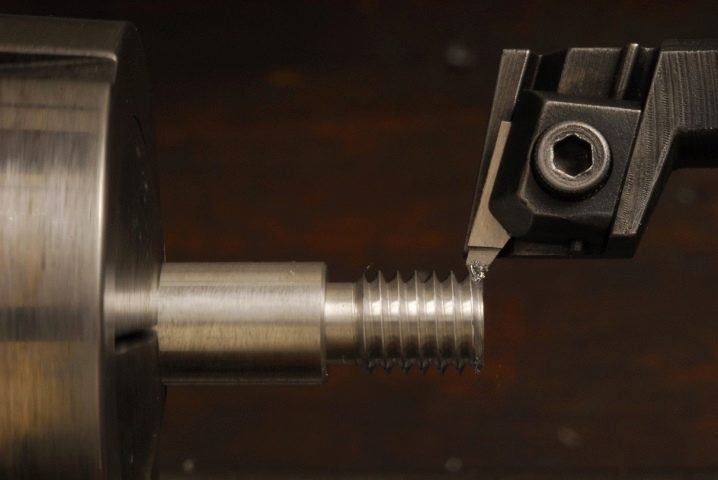
Der Kommentar wurde erfolgreich gesendet.