Wir stellen Maschinen zum Schärfen von Messern mit unseren eigenen Händen her
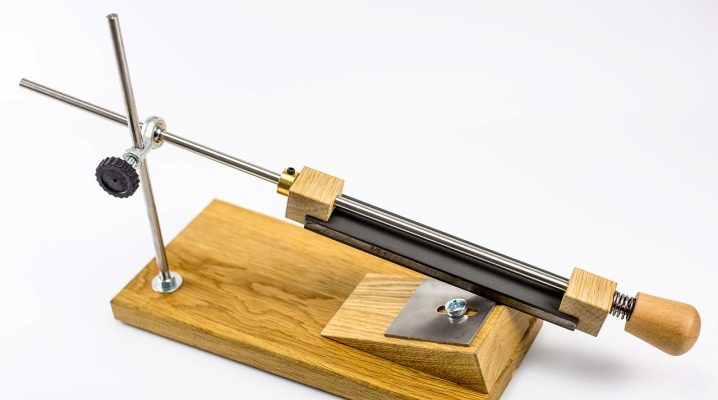
Messer leben nicht nur in der Küche - in einer Werkstatt, einem Jagdschloss werden sie auch zum Angeln benötigt. Ohne sie geht kaum eine Wanderung und es gibt tatsächlich viele Fälle, in denen man nicht darauf verzichten kann. Und wenn Messer oft verwendet werden – und es wäre schön, wenn sie immer perfekt geschärft wären – stellt sich die Frage nach der Notwendigkeit einer Schleifmaschine. Es ist nicht notwendig, es zu kaufen - Sie können eine Maschine mit Ihren eigenen Händen herstellen.
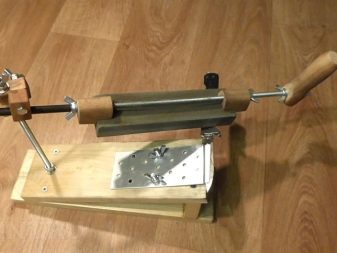
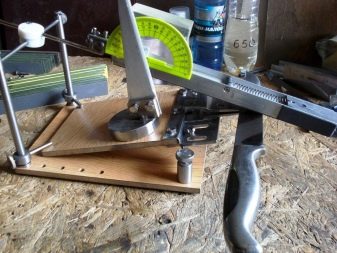
Einfache Herstellungsmethoden
Natürlich können Sie Messer von Hand schärfen, aber es wird schwierig sein, den richtigen Winkel beizubehalten, und daher ist die Qualität lahm. Aber beim Schärfen mit einer Maschine bleibt der ursprüngliche Winkel für den gesamten Arbeitsprozess erhalten, und neben der Hauptarbeit können Sie das Messer auch an der Maschine feinjustieren.
Die Hauptanforderung an eine selbstgebaute Werkzeugmaschine ist eine starre Fixierung von Klinge und Schleifmittel. Dadurch wird der Schärfwinkel erzeugt und beibehalten.
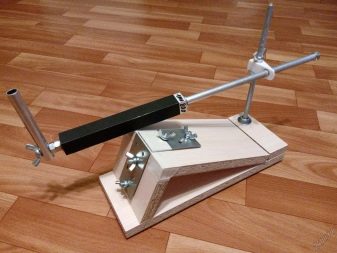
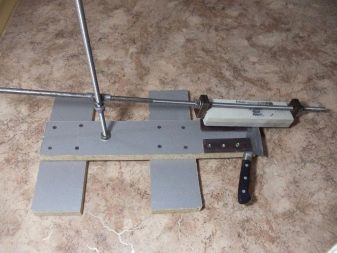
Aus den Ecken
Dies ist eine elementare vertikale Ausrüstung, die es ermöglicht, Messer schnell von Hand zu schärfen. Dies ist eine Holzkonstruktion mit einer Ecke.
Sie können es ohne genaue Zeichnungen tun, da die Abmessungen am Ende von den Abmessungen des Schleifsteins abhängen.
Was ist zu beachten, um eine manuelle Maschine zu erstellen:
- 4 Stäbe / Bretter 5–7 cm breit, 3 cm dick (die Länge der Diele entspricht der Länge des Steins);
- 4 Schrauben M4-M6 mit einem "Lamm", Sie können die Länge des Befestigungselements mit der Formel berechnen - die Dicke der Platte multipliziert mit zwei plus die Dicke des Schleifsteins plus 1 cm;
- 4 Blechschrauben für Holz - Dielenstärke minus 2 mm;
- Winkelmesser oder gleichwertig;
- bohren Sie mit einem Bohrer, um den Bolzen zu passen;
- Bügelsäge für Holz;
- Meißel;
- Marker.
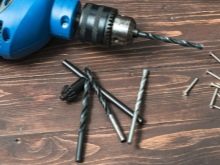
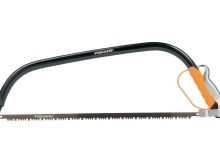
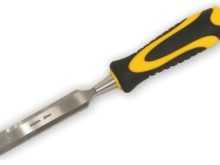
Die Maschine wird so gefertigt, dass aus den vorhandenen Brettern 2 Ecken gewonnen werden.
Beschreiben wir den Arbeitsfortschritt.
- Auf einer Diele wird in einem ihrer Breite entsprechenden Abstand ein Bügelsägenschnitt zur Mitte gemacht.
- Als nächstes müssen Sie vom Ende des Brettes den abgesägten Teil mit einem starken Messer oder Meißel abhacken. Die zweite Platine wird ebenfalls den gleichen Chip haben – beim Zusammenfügen der Platinen müssen beide Seiten eine gemeinsame Ebene haben.
- Die Dielen sind mit abgebrochenen Fragmenten zu einer Ecke gegliedert. Der zweite Teil der Einheit wird auf die gleiche Weise zusammengebaut.
- Im Ober- und Unterteil des Gerätes sind Schraubenlöcher gebohrt. Sie sind auf den Seiten gegenüber dem Verbindungspunkt der Enden markiert, auf jeder Platte befinden sich 3-4 Stück. Und die Löcher sind so markiert, dass von der Kante des Bretts bis zum äußeren Bolzen mindestens 3 cm vorhanden sind und der Spalt zwischen ihnen und anderen Löchern die Kante des Schleifsteins festklemmt.
- Auf der Innen- oder Außenseite eines Brettes wird eine Markierung angebracht, die jedem der möglichen Schärfwinkel entsprechen muss.
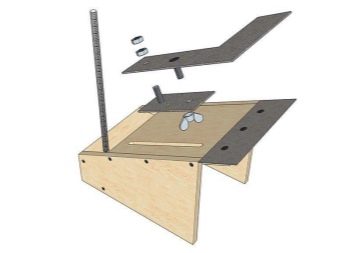
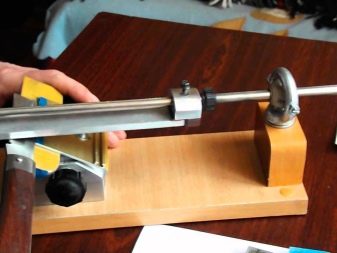
So arbeiten Sie mit einer solchen Maschine: Das geschärfte Messer wird mit der Klinge auf den Schleifstein gelegt, so dass sich die Klinge in einer vertikalen Ebene befindet. Außerdem bewegt sich das Messer bei hin- und hergehenden Bewegungen (dh "von sich selbst und zu sich selbst") mit einem sanften Druck entlang des Schmirgels.
Soll noch feiner geschärft werden, dann muss der Schärfstein zuerst mit Schleifpapier umwickelt werden. Das resultierende Gerät ist einfach und billig, aber mit der Befestigung des Steins ist nicht alles gut - andere Methoden helfen, die erforderliche Steifigkeit der Befestigung zu erreichen.
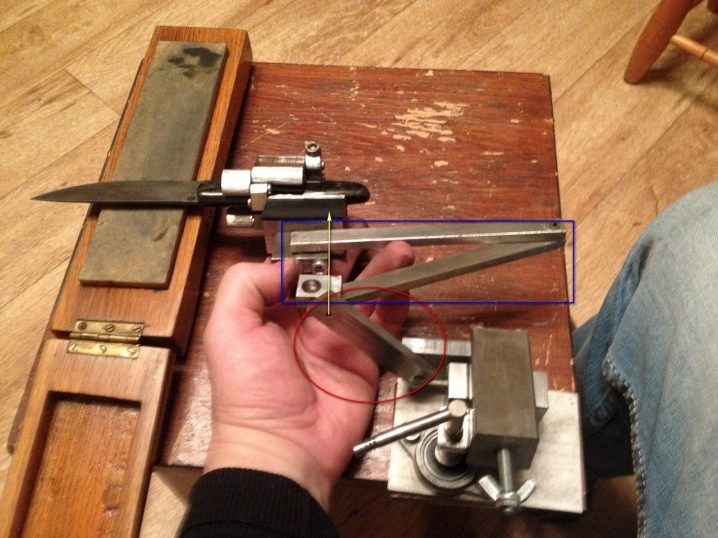
Sperrholz
Das Gerät wird kastenförmig sein, auf der einen Seite befindet sich eine Klingenfixierungseinheit, auf der anderen - eine Schlittenbefestigungsstange mit einem darauf befestigten Stein.
Was wird zur Anpassung benötigt:
- 2 Sperrholzplatten: die Dicke beträgt jeweils bis zu 10 mm (nicht weniger als 6), eine 23 cm x 4 cm, die andere 23 cm x 15 cm;
- 2 Holzblöcke (vorzugsweise Hartholz): einer - 15 cm x 5 cm x 5 cm, der zweite - 7 cm x 5 cm x 3 cm;
- 2 Karbolit-Niederhaltescheiben - 5 cm x 5 cm x 0,6 cm;
- 2 Stück Stahlblech 1 mm dick;
- 2 Möbelbeschläge;
- Sandpapier;
- Meißel;
- Bügelsäge für Metall;
- Winkelschleifer;
- bohren, bohren;
- Hammer;
- Schraubenzieher;
- Stiefelmesser;
- Schweißgerät mit Elektroden;
- Schrauben sowie Unterlegscheiben, Bolzen und Muttern.
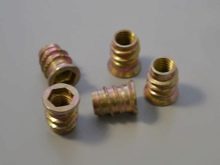
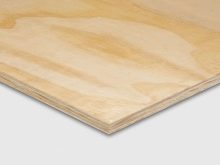
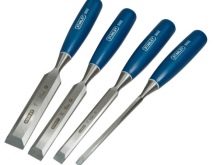
Hier ist der Prozess der Herstellung der Maschine in Etappen.
- Die Arbeit beginnt mit der Erstellung einer Sperrholz-Basisbox. Zuerst muss die Sperrholzplatte (die 23 cm x 4 cm) in zwei Teile gesägt werden. Es ist notwendig, entlang der langen Seite schräg zu schneiden, und so erhalten Sie am Ende 2 trapezförmige Teile mit den Maßen 23 cm x 3 cm x 1 cm. Wenn sich die Gelegenheit bietet, können Sie zwei Sperrholzstücke mit den angegebenen Abmessungen nehmen auf einmal, die die Seitenwände der Basis werden.
- Außerdem wird auf einer großen Sperrholzplatte, die 4 cm von der Kante entfernt ist, eine Nut gesägt. Sperrholzschichten werden entfernt, so dass eine 2 mm tiefe Nut entsteht. Nachdem die Enden mit Schleifpapier bearbeitet wurden, können Sie die Struktur zusammenbauen.
- Zuerst wird eine Seitenwand mit selbstschneidenden Schrauben an ein großes Blech geschraubt, dann die zweite. Und das Blatt wird so positioniert, dass die Auswahl vor der Basis liegt. Auf der Rückseite der Box ist ein Holzklotz mit selbstschneidenden Schrauben befestigt. In einem Abstand von 25 cm von der linken Seitenwand wird ein Loch in den Block gebohrt, dessen Durchmesser dem Durchmesser des Außengewindes des Gehäuses entspricht.
- Von unten und von oben ist es erforderlich, die Beschläge koaxial zueinander in die Leiste einzuschrauben. Dort wird der Einstellbolzen befestigt.
- Die Handschelle besteht aus Stahlplatten mit den Maßen 17 x 6 cm und 15 x 4 cm, die kleinere Platte wird auf die größere gelegt, 5–6 mm vom Rand entfernt, die Platten sind verschweißt. Bereits im zusammengebauten Aufbau sind 2 Löcher für die M4-M6 Schrauben angebracht. Dort werden Bolzen eingesetzt, die mit der Platte verschweißt werden. Der Schleifer kann Schweißperlen schneiden.
- Die Klemmleiste besteht aus zwei Teilen: Die Oberseite besteht aus einer Stahlplatte mit dem Buchstaben G, die Unterseite aus einem Rechteck. Die Platte besteht aus einem großen Teil von 15 x 8 cm und einem kleineren Teil von 5 x 4,5 cm Das Rechteck ist 10 x 5 cm groß Die L-förmige Platte muss so gelegt werden, dass ihr kleiner Teil die Handschellen bedeckt, aber nicht 3 cm² erreicht zu seinem äußeren Rand.
- Ein kleiner wird unter das lange Fragment der oberen Platte gelegt. Darin sind zwei Durchgangslöcher angebracht, die jeweils halb so groß wie die Bodenplatte sind. Die Platten selbst sind zu Bolzen verdreht. Die Köpfe der Schrauben sind mit ihren Platten verschweißt - und zwangsläufig "staffeln".
- Auf der Oberfläche der Base ist eine Linie parallel zu den Seitenwänden gezogen, sie verläuft entlang der Mitte der Füße, die an der Rückseite der Base in einer Leiste stehen. Von der Kante des oberen Fußes ist es notwendig, sich 4 cm zurückzuziehen, von der Kante der Hand - 2,5 cm - entlang der mit einer Stichsäge gezogenen Linie eine Nut mit einer Breite zu machen, die dem Durchmesser der Bolzen entspricht, die sind an die Platten geschweißt.
- Die Nut, in die die Befestigungselemente der Klemmleiste eingesetzt werden, wird justiert.
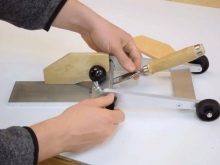
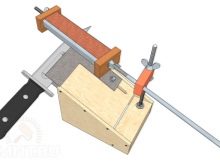
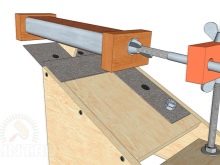
Wenn die Muttern gelöst sind, können Sie die Druckplatte zum Handschutz verschieben, Sie können sie davon wegbewegen, dh an einer solchen Maschine können Klingen jeder Breite bequem befestigt werden.
Getrennt davon lohnt es sich, das Einstellsystem einer solchen Maschine zu beschreiben. Dies ist ein vertikaler Bolzen in einem Stangenfuß, ein Stützblock, eine untere und eine obere Haltemutter. Der Zusammenbau des Systems sieht so aus: die Haarnadel wird in die Hülsen eingeschraubt, eine Unterlegscheibe wird darauf gelegt, eine Mutter wird aufgeschraubt. Die angezogene Mutter verhindert, dass sich der Stift um die Achse dreht. 1,6 cm von beiden Kanten der Stütze zurücktreten, wird ein Loch entlang der kürzeren Seite entlang des Durchmessers der Haarnadel gebohrt. Und das zweite Loch wird senkrecht zur Achse dieses Lochs mit einer Vertiefung von 4,5 cm gemacht. Nur mit einem doppelten Durchmesser des Stangenwagens. Die untere Einstellmutter wird auf den Stift geschraubt, der Schuh wird aufgesetzt, die obere Klemmmutter wird aufgeschraubt.
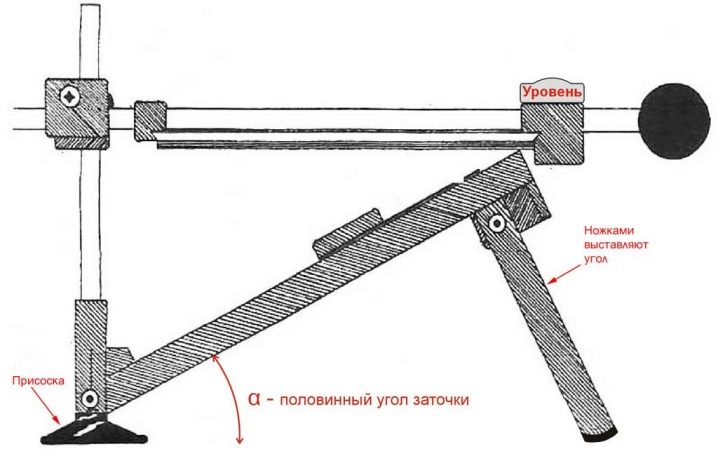
Und der Schleifwagen ist ein Metallstift mit einem Schleifstein. Von einem Ende des Bolzens wird eine Mutter aufgeschraubt, beide Niederhalter werden aufgesetzt, die zweite Mutter wird aufgeschraubt.Und sie sind so positioniert, dass der Schleifstein zwischen die Unterlegscheiben passt. Auf den Rest der Haarnadel wird ein Stück Plastikschlauch aufgesteckt (kann man einfach mit Isolierband machen). Das gegenüberliegende Ende des Bolzens wird in das Loch im Stützblock eingeführt.
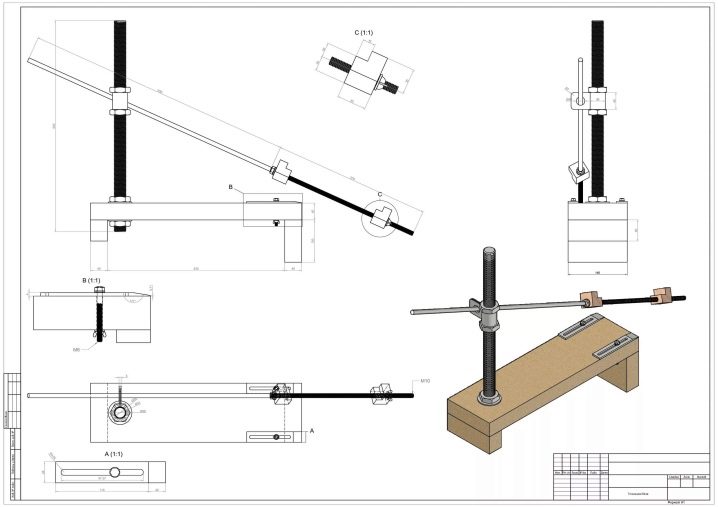
Wie baut man eine elektrische Maschine?
Um tatsächlich einen elektrischen Anspitzer selbst herzustellen, müssen Sie alles vorbereiten, was Sie brauchen.
Diese Liste enthält:
- unnötiges Laden bei 12 Volt;
- 12-Volt-Motor;
- Schalter;
- ein kleines Stück zweiadriger weicher Kupferdraht;
- runder Stein für einen Bohrer, 2 cm Durchmesser;
- Spannzangenfutter für die Motorachse;
- ein enges Rohrstück für einen Motor;
- 2 Schrauben.
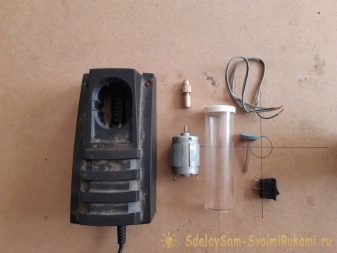
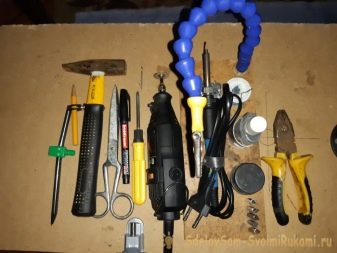
Von den Werkzeugen sind ein Lötkolben, ein Bohrer, ein Schraubendreher, eine Schere, eine Feile, ein Marker, ein Hammer und eine Zange nützlich.
Der Prozess zur Herstellung eines hausgemachten Anspitzers für Elektrowerkzeuge wird unten beschrieben.
- Zerlegen Sie das Ladegerät, wählen Sie einen Platz für den Schalter am Gehäuse und markieren Sie ihn mit einem Marker. Verwenden Sie einen Bohrer und eine Trennscheibe, um ein Loch zu schneiden. Richten Sie die Kanten mit einer Feile aus, probieren Sie den Schalter an.
- Schneiden Sie die Kupferdrähte der erforderlichen Länge ab, entfernen Sie das Geflecht von den Enden, tauchen Sie die Enden mit Zinn ein, löten Sie den Schalter an.
- Löten Sie einen Draht an die Ladekontaktklemme, den zweiten führen Sie durch das Gehäuseloch heraus. Der Draht wird angelötet bzw. an den zweiten Anschluss des Ladegeräts durch das zweite Loch für den Anschluss herausgeführt. Sie können das Gehäuse zusammenbauen.
- Löten Sie die Ausgangsdrähte an die Motorklemmen. Die Kanten der Metalleinlage mit einer Zange begradigen, 2 mm Löcher in die Ecken bohren. Es wird als Klemme verwendet, um den Motor gegen das Gehäuse zu halten. Der Motor wird mit einer Schelle mit geeigneten Schrauben an der Karosserie befestigt.
- Es ist notwendig, eine Schutzhülle vor Funken zu machen, die auch die Klinge fixiert - in diesem Fall wird eine Tube aus Verbundkleber verwendet. Die Spannzange wird zusammengebaut, ein flacher Stein wird zum Schärfen eingebaut, alles wird mit einer Zange festgezogen. Ein passendes Rohr wird oben auf den Motor gesteckt, die Stelle, wo der Schleifstein endet, ist mit einem Marker markiert.
- Mit einem Bohrer und einer Trennscheibe wird ein Schlitz gemacht, immer in einem Winkel, der für das Schärfen eines Messers relevant ist.
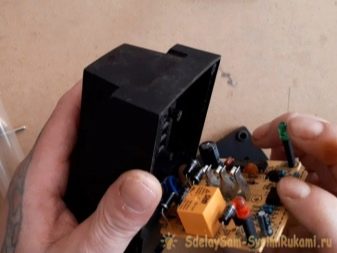
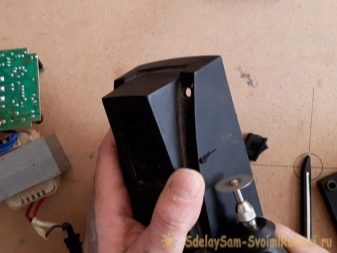
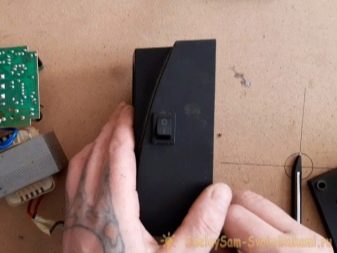
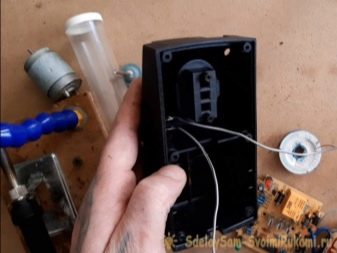
Es bleibt nur noch eine Gummimatte für die Mini-Maschine zu machen, da sie während des Betriebs klappert.
Bedienungstipps
So verwenden Sie die Maschine, damit die Messer richtig geschärft werden und die Person, die sie benutzt, sich nicht verletzt - alles wird in 5 grundlegenden Tipps behandelt.
- Alle Bewegungen mit einem Messer sollten nur glatt sein, keine Rucke, nichts schnelles, ohne Eile.
- Sie müssen gleichmäßig auf die Klinge drücken, und die genaue Kraft wird jeweils individuell entschieden.
- Die Klinge ist über die gesamte Länge gleichmäßig geschärft.
- Gegebenenfalls muss das Messer durch Eintauchen in Wasser gekühlt werden.
- Nach dem Schärfen kann die Klinge mit Schleifpapier (Körnung - nicht mehr als 800) geschliffen werden.
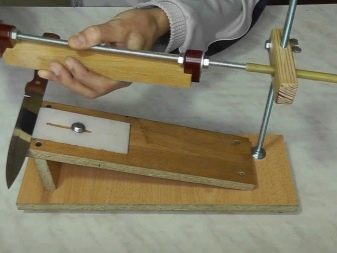
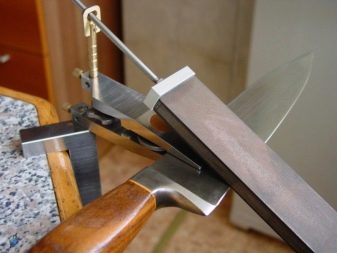
Sie können die Qualität des Schärfens wie folgt testen: Legen Sie ein Blatt Papier auf ein handelsübliches Schneidebrett, ziehen Sie ein Messer über das Blatt.
Bei schlechtem Schärfen reißt oder verbiegt sich das Blatt. Wenn es gut ist, ist es bewegungslos und gleichzeitig erscheint ein glatter Schnitt darauf. Alles ist einfach und klar.
Lassen Sie die selbstgebaute Maschine technisch perfekt sein und lange und mit hoher Qualität ihren Dienst tun!
Wie man Maschinen zum Schärfen von Messern mit eigenen Händen herstellt, sehen Sie im Video.
Der Kommentar wurde erfolgreich gesendet.