Einfädeln auf einer Drehmaschine
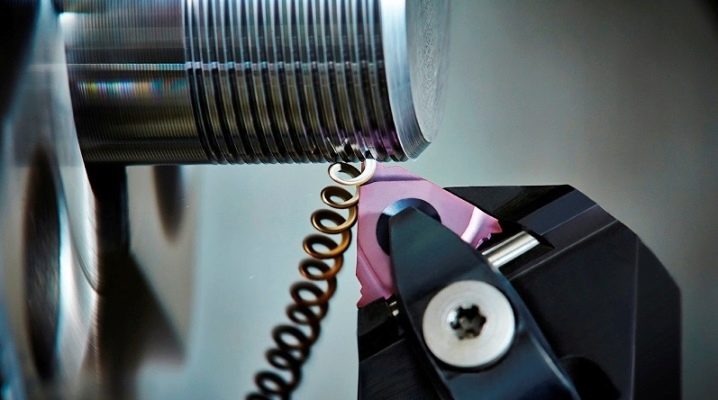
Das Gewindeschneiden mit einer Drehmaschine hat einen unbestreitbaren Vorteil: Der Durchsatz des Servicezentrums, in dem dieser Service praktiziert wird, erhöht sich um das 10-fache oder mehr. Außerdem macht die Maschine eine Größenordnung weniger Fehler als der Arbeiter.
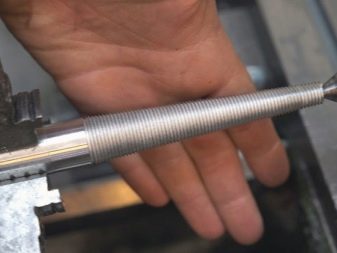
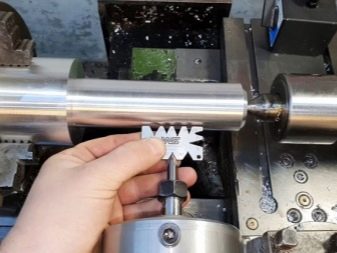
Gewindearten
Gewinderohlinge werden in Form von Zylindern und konischen (konischen) Bauteilen verwendet. Das Gewinde wiederum wird in Form einer Außenwendelnut (Spiralnut) oder als Innennut geschnitten. Der Aufbau einer Schraubverbindung wird durch ihr Profil bestimmt. In der Praxis werden mehrere Profiltypen verwendet:
- dreieckig;
- rechteckig;
- trapezförmig;
- aneinanderstoßend;
- gerundet.
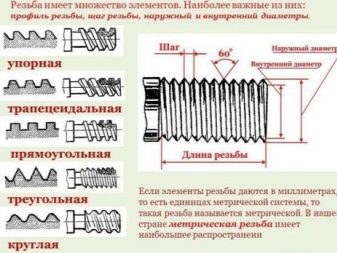
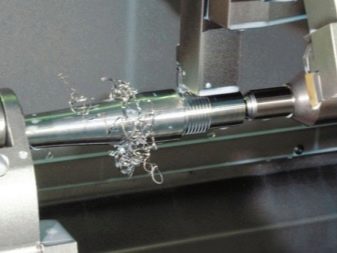
Wiederum, Gewindenuten werden in einem oder mehreren Durchgängen hergestellt. Im ersten Fall wird die Spiralnut in einer einzigen Version präsentiert: Nur ihre Windungen liegen nebeneinander, andere (begleitende) werden nicht verwendet. Die Gewindesteigung ist der Abstand zwischen den Mittelkanten (Aussparungen) der benachbarten Windungen. Der Verlauf der Gewindenut wird durch Multiplikation der Gewindesteigung mit der Anzahl der Windungen oder Steigungen mehrerer Nuten (bei mehreren Nuten) bestimmt.

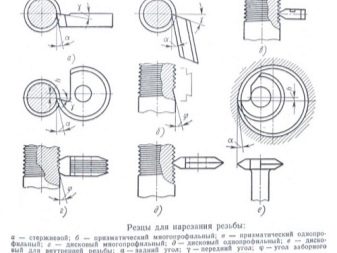
Nachdem Sie sich für die Art der Gewindeverbindung entschieden haben, werden die passenden Fräser ausgewählt. Ein solches Werkzeug ist eine Kombination aus einem Schaft und einem Arbeitsteil. Das Qualitätsniveau des Schraubengewindes wird durch die Leistung dieser Komponenten bestimmt. Der Schaft hat einen im Allgemeinen quadratischen oder regelmäßigen polyedrischen Querschnitt, um eine Zentrierung zu gewährleisten. Ohne Schaft ist es schwierig, den Fräser im Futter zu fixieren. Das Arbeitsteil schneidet eine spiralförmige Nut. Es umfasst Schnittflächen und scharfe Kanten. Der Schärfwinkel des Fräsers wird durch die Legierung bestimmt, aus der das Teil besteht. Hauptsächlich werden Stahl- und Buntmetallteile geschnitten. Nachdem sie den Schneidetyp ausgewählt haben, beginnen sie mit dem technologischen Prozess.
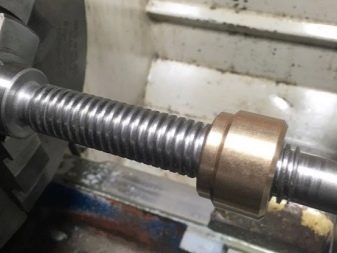
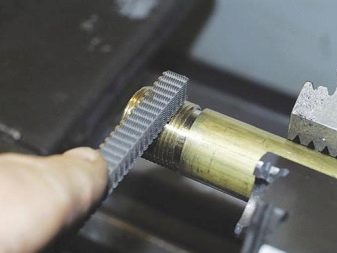
Schneidemethoden
Entlang der Drehachse hinterlässt der Fräser eine spiralförmige Nut auf dem Werkstück. Eines seiner Hauptmerkmale ist der Aufstiegs-(Aufstiegs-)Winkel. Der Winkel zwischen der gedachten Achse, die durch die Wendelnut verläuft, und der Ebene senkrecht zur Drehachse des Werkstücks wird entsprechend dem Wert des Brennervorschubs und der Drehzahl des Antriebs (Getriebe) berechnet. Die Größe der Gewindesteigung wird während der Bewegung entlang der Achse des zu schneidenden Werkstücks gemessen.
Als Ergebnis erhält der Cutter-Performer den Zuschnitt, den der Kunde bestellt hat. Beim Schneiden mehrerer Nuten (Minen) werden alle in Form von gleichmäßigen Spiralnuten angeordnet. Ein Beispiel für das Einfädeln eines mehrgängigen Gewindes sind PET-Flaschen und deren entsprechende Kunststoffkappen, beispielsweise für Sonnenblumenöl. Der Unterschied zwischen Flaschenverschlüssen und Bolzen und Muttern besteht darin, dass das Gewinde im ersten Fall kurz ist und nicht mehr als eine Umdrehung enthält.
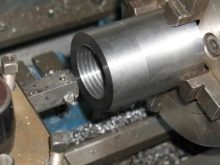
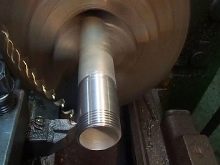
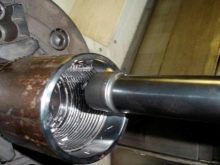
Die Gewindesteigung bei einer eingängigen Nut entspricht ihrer Steigung, während sie bei einem mehrgängigen Gewinde von der Anzahl koordinierter, aber unabhängiger Gewindegänge abhängt. Die Herstellung von Fräsern für ein- und mehrgängige Gewinde wird durch die Standards von GOST 18876-1973 geregelt. Das gleiche GOST schreibt das Schneiden von metrischen Gewinden vor, nicht von Zollgewinden. Nach diesen Normen werden Fräser in Form von Prismen-, Stab- und Rundfräsern hergestellt.
Das Außengewinde wird mit einem gebogenen Messer geschnitten, und das Innengewinde wird mit gerichteten und gebogenen Messern, die im Arbeitsrahmen befestigt sind, geschnitten. Die Brennerspitze ist identisch mit dem Profil der spiralförmigen Nut, die sie hinterlässt. Prismatische Fräser werden in Single- und Multi-Cut unterteilt.
Disk wird zusätzlich zu diesen beiden Varianten auch als separates Werkzeug für eine Innengewindenut hergestellt.
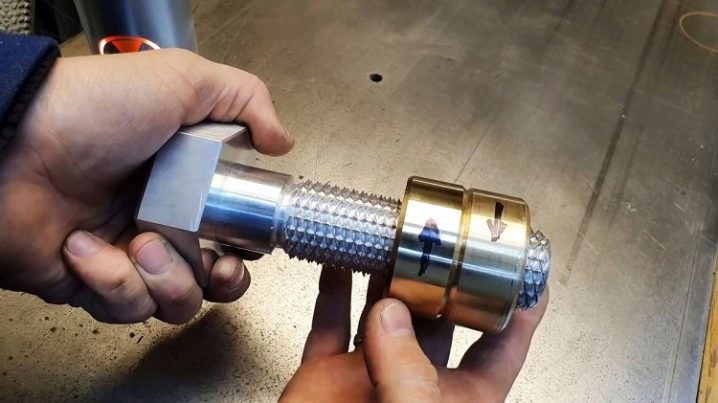
Schneidezähne
Dieses Design berücksichtigt wiederum die folgenden Parameter. Der Spanwinkel des Fräsers wird durch die Parameter des Materials bestimmt, aus dem das Teil geschnitten wird. Der Winkelwert liegt zwischen 0 und 250 Grad. Wenn die Nut an einfachen Stahllegierungsteilen mit mittlerem oder niedrigem Kohlenstoffgehalt bearbeitet wird, beträgt der Frontwinkel null. Je stärker der Stahl mit Legierungszusätzen gesättigt ist, desto größer wird der Winkel gewählt, darf aber in der Regel nicht mehr als 100 Grad betragen.
Eine Erhöhung der Schlagzähigkeit einer Stahllegierung erzwingt eine Erhöhung, eine Erhöhung der Härte und Sprödigkeit, im Gegensatz dazu, diesen Wert zu verringern. Wenn Sie den Winkel bei spröden Legierungen deutlich größer als Null lassen, treten Späne und Risse auf dem Teil auf. Es ist nicht akzeptabel, einen Fräser zu verwenden, der sich im Profil der Schneidkanten geringfügig von der Nut unterscheidet, die Sie in Zukunft benötigen werden.
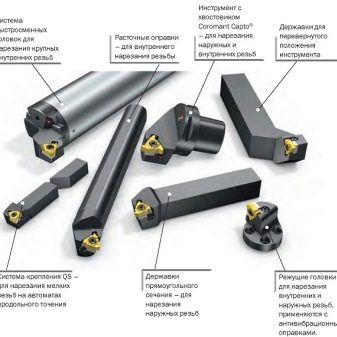
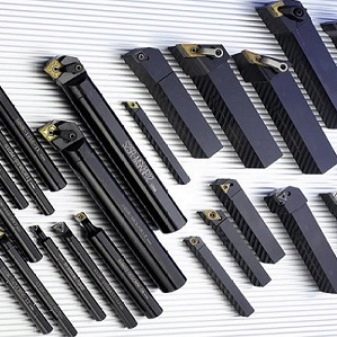
Die Winkel an der Rückseite und an den Seiten des Fräsers sind so gewählt, dass die Schneidzähne und Vorsprünge nicht an der Innenseite der gerade erhaltenen spiralförmigen Nut reiben. Trotz der Tatsache, dass als Arbeitsmaterial Schnellarbeitsstahl mit besonderer Härte verwendet wird, führt der Abrieb der scharfen Kanten allmählich zu deren Stumpfheit und der Fräser wird beschädigt.
Die Werte dieser Winkel werden auf beiden Seiten auf den gleichen Wert gesetzt. Wenn der Steigungswinkel, von dem die gute Beschaffenheit des Gewindes abhängt, kleiner als 4 Grad gewählt wird, sollten die Rückseitenwinkel auf einen Wert von 3 bis 50 eingestellt werden. Bei einem Winkel, der größer als . ist 4 Grad, die gleichen Winkel, die ihm entsprechen, stoppen bei einem Wert von 6 bis 8 Grad.
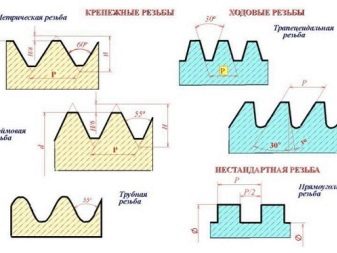
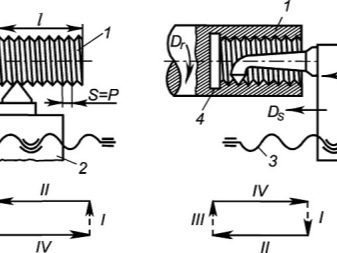
In vorgebohrte Löcher wird eine Innengewindenut geschnitten. Eine alternative Möglichkeit, Löcher zu machen, ist langweilig. Teile aus Stahl werden auf einer Maschine mit Hartmetalleinsätzen auf Basis der Stähle T15K6, T14K8, T15K6 oder T30K4 finalisiert. Beim Gewindeschneiden an einem Gusseisenwerkstück werden andere Hartmetallfräser verwendet: aus den Legierungen VK4, B2K, VK6M und VK3M.
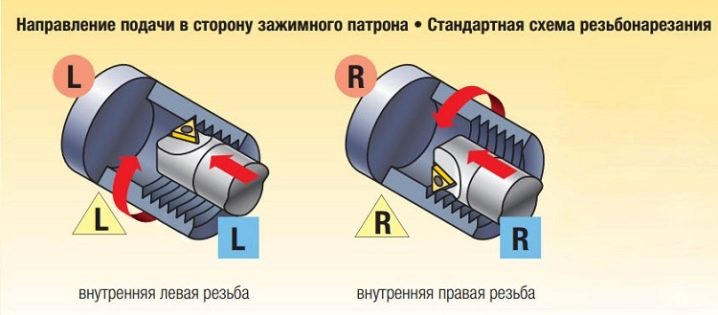
Matrizen und Hähne
Gewindebohrer und Matrizen sind Schraubenschlüssel- und Schraubenwerkzeuge, deren Innenfläche in Sektoren mit gleichem Abstand von der Mittelachse des Werkzeugs eingeschraubt ist. Benachbarte Abschnitte haben den gleichen Abstand voneinander. Die Drehmaschine wird hauptsächlich zum Schneiden von metrischen Gewinden verwendet. Auch die Fräser selbst unterscheiden sich nicht im großen Wert des Durchmessers der Werkstücke, für die sie ausgelegt sind. Im Falle der Verwendung von Schneidwerkzeugen, die für maschinelles Schneiden und nicht für manuelles Schneiden ausgelegt sind, erfolgt der Schneidvorgang in einem Schritt.
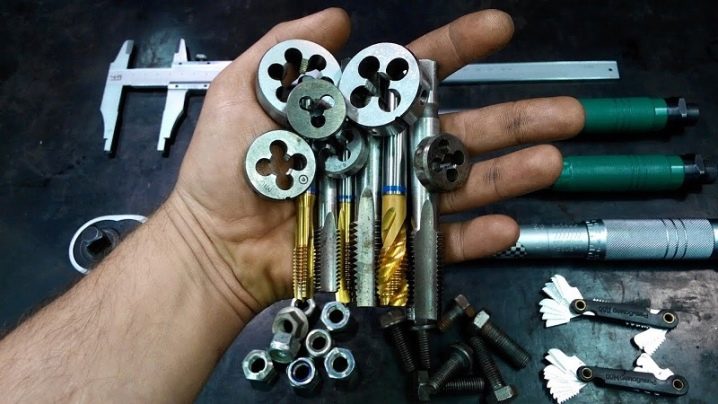
Der Unterschied zwischen Maschinengewindebohrern und einfachen manuellen Gewindebohrern besteht darin, dass auf ihnen Aufnahme- und Kalibrierarbeitszonen vorhanden sind. Bei der Verwendung herkömmlicher Fräser zum Gewindeschneiden kann der Handwerker nicht auf das Vorhandensein von ergänzenden Werkzeugen verzichten. In diesem Fall schneidet das erste Werkzeug das Gewinde grob und bewältigt 60 Prozent der Belastung, das zweite bringt diese Leistung auf 90 %, letzteres vollendet das Einstechen.
Diese Kombination kann sich ändern: Der Grobschnitt wird für drei Viertel des Gesamtarbeitsvolumens (Last) ausgeführt und der Endschnitt für das letzte Viertel. Die Aufnahmezone ist beim Schruppfräser deutlich länger als beim Schlichtfräser.
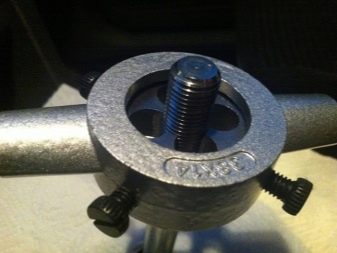
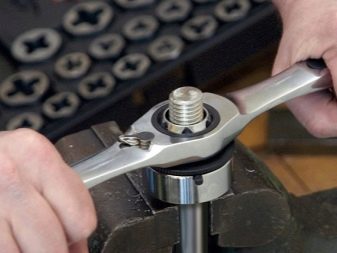
Der Durchsatz der Gewindeschneidmaschine variiert in folgenden Werten: bis zu 12 m der spiralförmigen Nut (und nicht die Länge des zu schneidenden Kanals oder Bolzens) pro Minute für Stahlrohlinge und bis zu 25 - für Gusseisen und alle Arten aus Buntmetall.
Bei Matrizen weicht der Durchmesser des Werkstücks nur um kleine Werte vom Ideal ab:
- 0,14-0,28 mm - für zukünftige Fäden mit einem Durchmesser von 20-30 mm;
- 0,12-0,24 mm - für einen Werkstückdurchmesser mit einem Gewinde von 11-18 mm;
- 0,1-0,2 mm - für Werkstücke mit einem Durchmesser von 6-10 mm.
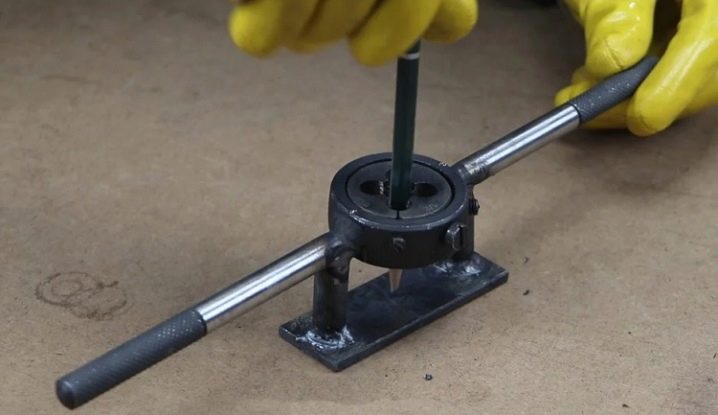
Die Matrizen sind in einem speziellen Halter im Futter des Spindelantriebs der Einheit eingebaut. In diesem Fall beträgt die Arbeitsgeschwindigkeit:
- 10-15 m pro Minute - für Nichteisenmetalle;
- 2-3 m pro Minute - für Gusseisen;
- 3-4 m pro Minute - für Stahlteile.
Für einen reibungslosen Sitz der Matrize auf dem Werkstück wird das zu schneidende Bolzenende auf eine Höhe von maximal einer Umdrehung des zukünftigen Gewindes angeschliffen. Das Schärfen sollte auf allen Seiten gleichmäßig sein, idealerweise erfolgt dies ebenfalls auf einer Drehbank.
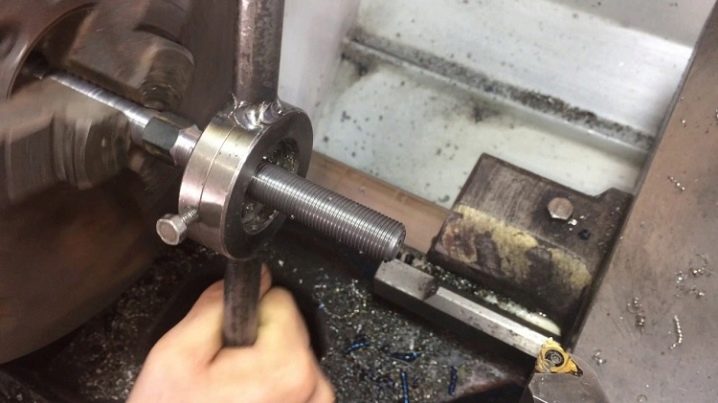
Kopf sterben
Das Gewindebohren mit einem Schneidkopf ist viel seltener als die Verwendung von Schneideisen und Gewindebohrern. Die Art der Gewindenut spielt keine Rolle. Der Arbeitsbereich des Kopfes ist die Kammkomponente. Prismenkämme werden hauptsächlich zum Innengewindeschneiden verwendet, während die Außennut mit einem radialen, abgerundeten oder tangentialen Werkzeug geschnitten wird. Das Funktionsprinzip basiert auf der Divergenz der Arbeitskomponenten beim Rückhub. Dank dieser Eigenschaft ist ein Kontakt mit der geschnittenen Nut vollständig ausgeschlossen. Das Kämmzubehör zum Innengewindeschneiden ist als ein Element mit Konus ausgeführt. Beim Schneiden eines Außengewindes werden Kammkomponenten mit abgerundetem Design verwendet, die einfache Elemente in der Ausführung sind.
Abgerundete Kämme können nachbearbeitet werden, um ihre Eigenschaften auf ihre ursprünglichen Werte zu bringen, von denen sie bei wiederholten Arbeitszyklen abweichen können. Beim Gewindeschneiden mit einer Drehmaschine, bei denen Schnecken- oder Schraubenelemente als Rohlinge deutlich länger als ursprünglich vorgesehen verwendet werden, montiert der Meister an der Sattelmontage des Drehmechanismus Gewindeschneidzubehör, was ihm ermöglicht, Aufträge mit größerem Volumen zu erfüllen .
Gewindeköpfe werden durch einfache Fräser oder topfförmige Elemente ergänzt.
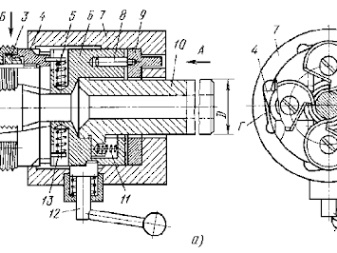
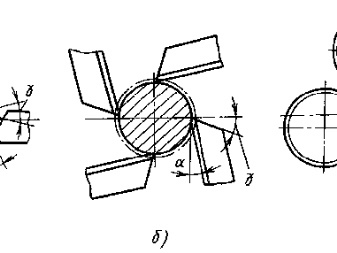
Häufige Fehler
Beim Drehen eines Gewindes auf einer Drehmaschine, egal ob links- oder rechtsgängig, sowie bei der Verwendung einer CNC-Werkzeugmaschine wird ein Schablonenwerkzeug verwendet, dank dem dieser Prozess auf eine breite fließen. Die ebene Komponente der Schablonenkomponente definiert die Steigung der Gewindenut. Kalibrierte Durchführungs- und Nicht-Zuführungskomponenten werden verwendet, um die vollständigste Kontrolle über das Schneiden zu erhalten. Das erste nimmt ein Profil mit einer Standardlänge an, das zweite ein verkürztes, mit dem Sie sicherstellen können, dass der durchschnittliche Durchmesser des Werkstücks konstant ist. Unachtsames Arbeiten führt bei nachlässiger Behandlung zur Bildung von Fehlern auf der rauen Oberfläche.
Überprüfen Sie nach der Bearbeitung des Teils (Bewehrung, Rohrknüppel) den Durchmesser mit einem Gewindemikrometer. Dieses Instrument sollte nach einem Referenzmuster eingerichtet werden, um die Genauigkeit des Tests zu gewährleisten. Bevor Sie überprüfen, ob das Gewinde mit dem angegebenen Durchmesser übereinstimmt, reinigen Sie die Nut und den Schmutz, den Sie gerade mit dem Werkzeug gemacht haben.
Verwenden Sie unbedingt Industrie- oder Motoröl. Verwenden Sie das Werkzeug nicht trocken, da eine Überhitzung von Matrize, Gewindebohrer oder Gewindekopf den verwendeten Brenner beschädigt. Selbst siegreiche Werkzeuge mit Diamantkörnung verschlechtern sich, wenn die Hitze ab 900 Grad freigesetzt wird.
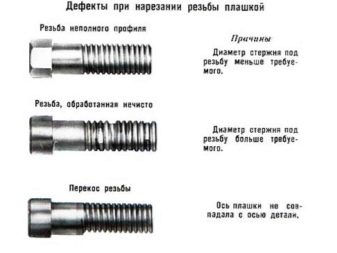
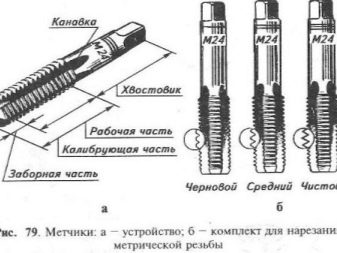
Informationen zum Schneiden von Gewinden auf einer Drehmaschine finden Sie im nächsten Video.
Der Kommentar wurde erfolgreich gesendet.