Alles über Kohlefaser

Für jeden modernen Menschen ist es sehr wichtig, alles über Kohlefaser zu wissen. Wenn Sie die Technologie der Kohlenstoffproduktion in Russland, die Dichte und andere Eigenschaften von Kohlenstofffasern verstehen, wird es einfacher sein, den Anwendungsbereich zu verstehen und die richtige Wahl zu treffen. Außerdem sollten Sie alles über Spachtelmasse und Fußbodenheizung mit Kohlefaser, über ausländische Hersteller dieses Produkts und über verschiedene Anwendungsgebiete erfahren.


Besonderheiten
Die Bezeichnungen Kohlefaser und Kohlefaser, in einigen Quellen auch Kohlefaser, sind weit verbreitet. Aber die Vorstellung von den tatsächlichen Eigenschaften dieser Materialien und den Möglichkeiten ihrer Verwendung ist für viele Menschen ganz anders. Aus technischer Sicht ist Dieses Material besteht aus Fäden mit einem Querschnitt von nicht weniger als 5 und nicht mehr als 15 Mikrometer... Fast die gesamte Zusammensetzung besteht aus Kohlenstoffatomen - daher der Name. Diese Atome selbst sind zu scharfen Kristallen gruppiert, die parallele Linien bilden.


Diese Konstruktion bietet eine sehr hohe Zugfestigkeit. Kohlefaser ist keine völlig neue Erfindung. Die ersten Muster eines ähnlichen Materials wurden von Edison erhalten und verwendet. Später, Mitte des 20. Jahrhunderts, erlebte die Kohlefaser eine Renaissance – und seitdem hat ihr Einsatz stetig zugenommen.
Kohlefaser wird mittlerweile aus ganz anderen Rohstoffen hergestellt – und daher können ihre Eigenschaften stark variieren.


Zusammensetzung und physikalische Eigenschaften
Die wichtigste Eigenschaft von Kohlefaser bleibt ihre außergewöhnliche Hitzebeständigkeit... Selbst wenn die Substanz auf 1600 - 2000 Grad erhitzt wird, ändern sich ihre Parameter in Abwesenheit von Sauerstoff in der Umgebung nicht. Die Dichte dieses Materials ist neben dem üblichen auch linear (gemessen im sogenannten Tex). Bei einem Titer von 600 tex beträgt die Masse von 1 km Bahn 600 g. In vielen Fällen ist auch der Elastizitätsmodul des Materials, oder wie man sagt, der Youngsche Modul von entscheidender Bedeutung.
Für hochfeste Fasern reicht dieser Wert von 200 bis 250 GPa. Hochmodulige Kohlefasern auf Basis von PAN haben einen Elastizitätsmodul von ca. 400 GPa. Bei Flüssigkristalllösungen kann dieser Parameter von 400 bis 700 GPa variieren. Der Elastizitätsmodul wird basierend auf der Schätzung seines Wertes berechnet, wenn einzelne Graphitkristalle gestreckt werden. Die Orientierung der Atomebenen wird mittels Röntgenbeugungsanalyse ermittelt.


Die Standardoberflächenspannung beträgt 0,86 N / m. Bei der Verarbeitung des Materials zu einer Metallverbundfaser steigt dieser Wert auf 1,0 N/m. Die Messung nach der Kapillaraufstiegsmethode hilft, den entsprechenden Parameter zu bestimmen. Die Schmelztemperatur von Fasern auf Basis von Erdölpechen beträgt 200 Grad. Das Spinnen findet bei etwa 250 Grad statt; der Schmelzpunkt anderer Faserarten hängt direkt von ihrer Zusammensetzung ab.
Die maximale Breite von Carbongeweben hängt von technologischen Anforderungen und Nuancen ab. Bei vielen Herstellern sind es 100 oder 125 cm. Die axiale Festigkeit ist gleich:
- für hochfeste Produkte auf Basis von PAN von 3000 bis 3500 MPa;
- für Fasern mit signifikanter Dehnung streng 4500 MPa;
- für hochmoduliges Material von 2000 bis 4500 MPa.


Theoretische Berechnungen der Stabilität eines Kristalls unter einer Zugkraft in Richtung der Atomebene des Gitters ergeben einen geschätzten Wert von 180 GPa.Der erwartete praktische Grenzwert liegt bei 100 GPa. Experimente haben jedoch das Vorhandensein eines Niveaus von mehr als 20 GPa noch nicht bestätigt. Die wirkliche Festigkeit von Kohlefaser wird durch ihre mechanischen Defekte und die Nuancen des Herstellungsprozesses begrenzt. Die in praktischen Studien ermittelte Zugfestigkeit eines Profils mit einer Länge von 1/10 mm beträgt 9 bis 10 GPa.
Besondere Aufmerksamkeit verdient die T30 Kohlefaser. Dieses Material wird hauptsächlich bei der Herstellung von Stangen verwendet. Diese Lösung zeichnet sich durch ihre Leichtigkeit und ausgezeichnete Balance aus. Der T30-Index bezeichnet einen Elastizitätsmodul von 30 Tonnen.
Komplexere Herstellungsprozesse ermöglichen es Ihnen, ein Produkt der Stufe T35 usw. zu erhalten.


Produktionstechnologie
Kohlefasern können aus einer Vielzahl von Polymertypen hergestellt werden. Der Verarbeitungsmodus bestimmt zwei Haupttypen solcher Materialien - karbonisierte und graphitisierte Typen. Ein wichtiger Unterschied besteht zwischen Fasern, die von PAN abgeleitet sind, und verschiedenen Pechtypen. Qualitätskohlenstofffasern, sowohl in hochfesten als auch in hochmoduligen Qualitäten, können unterschiedliche Härte- und Modulniveaus aufweisen. Es ist üblich, sie auf verschiedene Marken zu verweisen.
Fasern werden im Filament- oder Bündelformat hergestellt. Sie werden aus 1000 bis 10000 Endlosfilamenten gebildet. Aus diesen Fasern können auch Gewebe hergestellt werden, wie beispielsweise Kabel (in diesem Fall ist die Anzahl der Filamente noch größer). Ausgangsrohstoff sind nicht nur einfache Fasern, sondern auch Flüssigkristallpeche sowie Polyacrylnitril. Der Produktionsprozess beinhaltet zunächst die Herstellung der ursprünglichen Fasern, die dann an der Luft auf 200 - 300 Grad erhitzt werden.

Im Fall von PAN wird dieser Prozess als Vorbehandlung oder Feuerwiderstandsverbesserung bezeichnet. Nach einem solchen Verfahren erhält Pech eine so wichtige Eigenschaft wie Unschmelzbarkeit. Die Fasern sind teilweise oxidiert. Die Art der weiteren Erwärmung bestimmt, ob sie zur karbonisierten oder zur graphitierten Gruppe gehören. Das Ende der Arbeit bedeutet, der Oberfläche die erforderlichen Eigenschaften zu verleihen, danach wird sie fertiggestellt oder kalibriert.
Die Oxidation an der Luft erhöht die Feuerbeständigkeit nicht nur durch Oxidation. Dazu tragen nicht nur die partielle Dehydrierung, sondern auch die intermolekulare Vernetzung und andere Verfahren bei. Außerdem wird die Anfälligkeit des Materials gegenüber Schmelzen und Verflüchtigung von Kohlenstoffatomen verringert. Die Karbonisierung (in der Hochtemperaturphase) geht mit einer Vergasung und dem Entweichen aller Fremdatome einher.
PAN-Fasern, die in Gegenwart von Luft auf 200 - 300 Grad erhitzt werden, werden schwarz.


Ihre anschließende Karbonisierung erfolgt in einer Stickstoffumgebung bei 1000 - 1500 Grad. Laut einer Reihe von Technologen beträgt die optimale Heizstufe 1200 - 1400 Grad. Hochmodulfasern müssen auf etwa 2500 Grad erhitzt werden. In der Vorstufe erhält PAN eine Leitermikrostruktur. Die Kondensation auf intramolekularer Ebene, begleitet vom Auftreten eines polyzyklischen Aromastoffes, ist für deren Auftreten "verantwortlich".
Je mehr die Temperatur ansteigt, desto größer wird die Struktur des zyklischen Typs. Die Anordnung der Moleküle bzw. aromatischen Fragmente erfolgt nach Beendigung der Wärmebehandlung gemäß der Technologie so, dass die Hauptachsen parallel zur Faserachse verlaufen. Die Spannung verhindert ein Abfallen des Orientierungsgrades. Die Besonderheiten der PAN-Zersetzung während der Wärmebehandlung werden durch die Konzentration der gepfropften Monomere bestimmt. Jeder Typ solcher Fasern bestimmt die anfänglichen Verarbeitungsbedingungen.

Flüssigkristall-Erdölpech muss lange Zeit bei Temperaturen von 350 bis 400 Grad aufbewahrt werden. Dieser Modus führt zur Kondensation polyzyklischer Moleküle. Ihre Masse nimmt zu und es kommt allmählich zum Zusammenkleben (unter Bildung von Sphärolithen). Wenn die Erwärmung nicht aufhört, wachsen die Sphärolithe, das Molekulargewicht nimmt zu und das Ergebnis ist die Bildung einer kontinuierlichen flüssigkristallinen Phase. Kristalle sind gelegentlich in Chinolin löslich, aber normalerweise lösen sie sich weder darin noch in Pyridin (dies hängt von den Nuancen der Technologie ab).
Fasern, die aus Flüssigkristallpech mit 55 - 65 % Flüssigkristallen gewonnen werden, fließen plastisch. Das Spinnen wird bei 350 - 400 Grad durchgeführt. Eine stark orientierte Struktur wird durch anfängliches Erhitzen in einer Luftatmosphäre bei 200 - 350 Grad und anschließendes Halten in einer inerten Atmosphäre gebildet. Fasern der Marke Thornel P-55 müssen auf bis zu 2000 Grad erhitzt werden, je höher der Elastizitätsmodul, desto höher sollte die Temperatur sein.



In letzter Zeit widmen wissenschaftliche und technische Arbeiten der Technologie, die Hydrierung verwendet, immer mehr Aufmerksamkeit. Die anfängliche Herstellung von Fasern wird oft durch Hydrieren einer Mischung aus Kohlenteerpech und Naphthalingummi erreicht. In diesem Fall sollte Tetrahydrochinolin vorhanden sein. Die Verarbeitungstemperatur beträgt 380 - 500 Grad. Feststoffe können durch Filtration und Zentrifuge entfernt werden; dann werden die Peches bei erhöhter Temperatur verdickt. Für die Herstellung von Carbon ist es notwendig, (je nach Technologie) ganz unterschiedliche Geräte zu verwenden:
- Schichten, die das Vakuum verteilen;
- Pumps;
- Abdichtgeschirre;
- Arbeitstische;
- Fallen;
- leitfähiges Netz;
- Vakuumfolien;
- Prepregs;
- Autoklaven.


Marktüberblick
Die folgenden Kohlefaserhersteller sind auf dem Weltmarkt führend:
- Thornell, Fortafil und Celion (USA);
- Grafil und Modmore (England);
- Kureha-Lone und Toreika (Japan);
- Cytec-Industrien;
- Excel;
- SGL-Gruppe;
- Toray-Industrien;
- Zoltek;
- Mitsubishi Rayon.


Heute wird Kohlenstoff in Russland produziert:
- Tscheljabinsk-Werk von Kohlenstoff und Verbundwerkstoffen;
- Balakovo-Kohlenstoffproduktion;
- NPK Khimprominzhiniring;
- Saratow-Unternehmen "START".
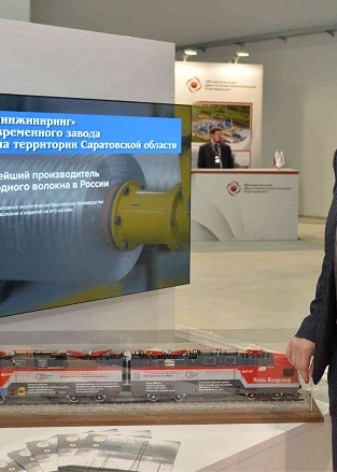

Produkte und Anwendungen
Kohlefaser wird verwendet, um Verbundverstärkungen herzustellen. Es ist auch üblich, es zu verwenden, um Folgendes zu erhalten:
- bidirektionale Stoffe;
- Designerstoffe;
- biaxiales und quadroaxiales Gewebe;
- Vlies;
- unidirektionales Band;
- Prepregs;
- externe Verstärkung;
- Faser;
- Gurte.

Eine ziemlich ernstzunehmende Neuerung ist jetzt Infrarot warmer Boden. In diesem Fall wird das Material als Ersatz für den herkömmlichen Metalldraht verwendet. Es kann dreimal mehr Wärme erzeugen, außerdem wird der Energieverbrauch um ca. 50% reduziert. Liebhaber komplexer Techniken verwenden oft Kohlenstoffrohre, die durch Wickeln gewonnen werden. Diese Produkte werden auch von Herstellern von Autos und anderen Geräten nachgefragt. Kohlefaser wird beispielsweise häufig für Handbremsen verwendet. Auf der Grundlage dieses Materials erhalten Sie außerdem:
- Teile für Flugzeugmodelle;
- einteilige Hauben;
- Fahrräder;
- Teile für das Tuning von Autos und Motorrädern.


Carbongewebeplatten sind 18 % steifer als Aluminium und 14 % mehr als Baustahl... Auf diesem Material basierende Muffen werden benötigt, um Rohre und Rohre mit variablem Querschnitt, spiralförmige Produkte mit verschiedenen Profilen zu erhalten. Sie werden auch zur Herstellung und Reparatur von Golfschlägern verwendet. Erwähnenswert ist auch die Verwendung. bei der Herstellung besonders strapazierfähiger Hüllen für Smartphones und andere Gadgets. Solche Produkte sind in der Regel von erstklassiger Natur und haben verbesserte dekorative Eigenschaften.
Was das dispergierte Pulver vom Graphittyp betrifft, wird Folgendes benötigt:
- beim Empfangen von elektrisch leitfähigen Beschichtungen;
- beim Lösen von Klebstoffen verschiedener Art;
- beim Verstärken von Formen und einigen anderen Teilen.


Kohlefaserspachtel ist in vielerlei Hinsicht besser als herkömmlicher Spachtel. Diese Kombination wird von vielen Experten wegen ihrer Plastizität und mechanischen Festigkeit geschätzt. Die Zusammensetzung ist zum Abdecken tiefer Defekte geeignet. Carbon-Ruten oder -Ruten sind stark, leicht und langlebig. Dieses Material wird benötigt für:
- Luftfahrt;
- die Raketenindustrie;
- Ausgabe von Sportgeräten.
Durch Pyrolyse von Carbonsäuresalzen können Ketone und Aldehyde erhalten werden.Die hervorragenden thermischen Eigenschaften von Kohlefaser ermöglichen den Einsatz in Heizungen und Heizkissen. Solche Heizungen:
- wirtschaftlich;
- zuverlässig;
- zeichnen sich durch beeindruckende Effizienz aus;
- keine gefährliche Strahlung verbreiten;
- relativ kompakt;
- perfekt automatisiert;
- ohne unnötige Probleme betrieben;
- keine Fremdgeräusche verbreiten.


Kohlenstoff-Kohlenstoff-Verbundwerkstoffe werden verwendet bei der Herstellung von:
- Halterungen für Tiegel;
- konische Teile für Vakuumschmelzöfen;
- Rohrteile für sie.
Weitere Anwendungsgebiete sind:
- hausgemachte Messer;
- Verwendung für ein Blütenblattventil an Motoren;
- im Bauwesen verwenden.
Moderne Bauherren verwenden dieses Material seit langem nicht nur zur Außenverstärkung. Es wird auch benötigt, um Steinhäuser und Schwimmbäder zu stärken. Die geklebte Verstärkungsschicht stellt die Qualitäten von Stützen und Trägern in Brücken wieder her. Es wird auch beim Erstellen von Klärgruben und beim Einrahmen natürlicher, künstlicher Reservoirs verwendet, wenn mit einem Senkkasten und einer Silogrube gearbeitet wird.
Sie können auch Werkzeuggriffe reparieren, Rohre reparieren, Möbelbeine, Schläuche, Griffe, Gerätekoffer, Fensterbänke und PVC-Fenster reparieren.


Im nächsten Video finden Sie weitere Informationen zur Herstellung von Kohlefaser.
Der Kommentar wurde erfolgreich gesendet.